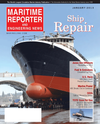
Page 13: of Maritime Reporter Magazine (January 2013)
Ship Repair & Conversion
Read this page in Pdf, Flash or Html5 edition of January 2013 Maritime Reporter Magazine
WWW.MARINELINK.COM 132008, we doubled our business every year. It sounds pretty drastic. But that?s the shipyard busi- ness ? it has always been cyclical, and it always will be.What do you consider to be the great-est challenges to running a profitable business? The biggest factor is regula- tory; everything having to with gov-ernment regulations is probably the biggest challenge, and unfortunately even health care is a part of that to-day. The toughest thing that we face year-in, year-out is how to deal with the regulatory issues: environmental, safety, health care, accounting ? ev- erything.So you started the business in 1998. How exactly did you come to be in the marine industry? I grew up operating boats, as both my dad and my uncle owned tugs and barge, operating inland to offshore. They were at the forefront of ATB development in the mid-70s. (The first Bludworth ATB Flexible Pushing System entered service in 1970. For decades Bludworth lead the field in US ATB tug & barge ap- plications). I?ve spent most of my life operating tugs and barges, mostly offshore. I chose to not get into that business myself because it?s too tough from a regulatory perspective and heavily capital intensive for a start up.Why did you start your own business? It?s what I always wanted to do, so I jumped off and started it part time. I kept my regular job for a cou-ple of years, and when it came time to split, we split, and they (Martin Ma-rine) are still one of my better custom-ers. They were on board with what I was doing.So how does the upcoming year look? Our sales will be down sim- ply because we don?t have any new construction projects in the pipeline, but the repair business is much more reliable in terms of making or los-ing money. New construction is tight margin business. But it?s still good in terms of balancing your workforce.Can you tell us about one of the toughest or most challenging ship re-pair jobs you?ve ever encountered? I got a call one day saying that a steel ingot had fallen through a ship (courtesy of a broken chain), right here in Houston. It was stuck like a knife blade through the double bottom. That ingot was 40 ft. long, 8 inches thick, 8 feet wide. They were lifting the ingots out, the chain broke and the ingot went right through the ship like a knife. It was sticking 8 to 10 feet below the ship, and the rest of it was in the cargo hold. No one was hurt, but the forklift didn?t make it. That said, having all of your facilities under water in the wake of Hurricane Ike was quite a challenge too. We had zero sales for 3 months, as that was recovery time. That was a tough one. We survived because we had enough cash in the bank. It?s that simple. MR #1 (10-17).indd 13MR #1 (10-17).indd 131/2/2013 10:13:59 AM1/2/2013 10:13:59 AM