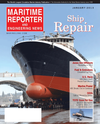
Page 37: of Maritime Reporter Magazine (January 2013)
Ship Repair & Conversion
Read this page in Pdf, Flash or Html5 edition of January 2013 Maritime Reporter Magazine
WWW.MARINELINK.COM 37While it may come as a surprise to some that the world?s Þ rst LNG-powered containership will be built in a U.S. shipyard, it should come as a surprise to none that the U.S. shipyard selected is General Dynamics NASSCO in San Diego, Calif.In the massive consolidation of big shipbuilding prowess which has swept the U.S. industry over the past decade, NASSCO has emerged as a clear leader in ship construction and repair for both the U.S. Navy as well as commercial customers. While part of the credit lies with the shipyard?s strategic alignment with leading commercial shipbuilders in South Korea, the lion?s share resides within the yard itself, which has fol-lowed a steady course facility and per- sonnel investment and improvement to help reduce costs while increasing qual-ity. ?As you are aware, General Dynam-ics NASSCO is the only full-service shipbuilding and repair yard on the West Coast of the U.S.,? said Fred Harris, President, NASSCO. ?We aggressively pursue continuous process improve-ments to reduce product cost and cycle times on each of our shipbuilding and repair programs. NASSCO has taken a systematic approach to reduce the cost of producing new ships while still deliv-ering a quality product. This approach addresses our production facilities, our design processes, and ultimately, those activities taking place at the deck plate level in the shipyard. Looking to the future, we are examining how to further improve total cost of ownership for our customer. According to Harris, there are essen-tially three means the yard is working at to this end.1. MODIFYING FACILITIES The systematic approach NASSCO has taken to continuous improvement began with a complete assessment of the shipyard facility in 2005-2006. The focus of this capital investment was to provide ample lay down space for the outÞ tting of large ship blocks and grand blocks, prior to their erection into a grav-ing dock or building ways. The com- pany invested approximately $150m in facility improvements between 2006 and 2009. The expenditures made on these capital investments came as a direct result of NASSCO?s relationship with world-class Korean shipbuilders and as-sociated benchmarking of capabilities accomplished through GAP analysis. Major renovations to NASSCO?s facil- ity during this time included the estab-lishment of a fully-enclosed, onsite blast and paint facility, and the addition of a new intermediary stage of construction known as Stage of Construction 4 (SOC 4). The integration of General Dynam-ics Marine Systems Group principles brought the thought process of moving the Þ nal State of Construction 6 (SOC 6) work to earlier stages of construction at NASSCO. In early stages of ship-building production, it is cheaper and easier to redesign the product so that it is more producible. Prior to bringing these producibility measures to produc-tion, all cost reduction measures resided in the engineering and planning phases at NASSCO. By bringing cost reduction measures to production, the number of man-hours required to build each ship was reduced by improving efÞ ciencies in touch labor. 2. LESSONS LEARNED, LEAN SIX SIGMA, AND PROCESS IMPROVEMENT INITIATIVES The introduction of Lean Six Sigma (LSS) to the modernized shipbuilding processes now in place at NASSCO allowed for the modiÞ cation of these processes for better efÞ ciency. This ef- fort looked at processes from supplier to end user, exposing hidden produc- tivity gains in material handling and processes aimed at reducing rework. Similarly, the Process Improvement Initiative (PII) Program unleashed the capability of NASSCO?s workforce by having employees focus on and speak up about what they can do to improve their jobs on a daily basis. Individuals at the deck plate level who best know the intricacies of what their tasks entail can provide the best input. Today, we now have 3,000 employees now working to reduce cost at NASSCO. Of the 10,000 employee ideas submitted to the PII Pro-gram in 2010, 75% were implemented. This year, we expect to have more than 20,000 ideas submitted, with 90% of them incorporated into our processes. With the implementation of the PII pro- gram, NASSCO has multiplied the num-ber of people thinking about cost saving in the shipyard by tenfold. The entire enterprise is now involved in cost reduc-tions, whereas before it was focused in Engineering and Planning. 3. CONSIDERING TOTAL OWNERSHIP COSTS The three tenets of NASSCO shipbuild-ing are: (1) get the design process down; (2) know how you are going to build the ship (i.e. facility considerations); and (3) get the design and planning done prior to the start of construction, with all con-struction material available prior to start of construction.NASSCO realized that the costs as-sociated with producing naval and com-mercial vessels can be greatly improved by the efÞ ciencies of the shipbuilder. It is estimated that 85% of the total own-ership cost for a ship over its lifetime is formed at the earliest design phases. Currently, NASSCO and the U.S. Navy have established a partnership in which to openly discuss reducing costs at the acquisition phase. In our commercial shipbuilding activities, NASSCO works closely with our customers throughout each step of the design and construction phase to ensure that further cost saving considerations will be realized over the total life of the ship. NASSCO envi-sions that these discussions will be ex-panded on the TOTE contract, given that this shipbuilding program is a Þ rst-of-its-kind in the Þ eld of LNG propulsion. Shipbuilding by Numbers ? Easy as ?1, 2, 3?WWW.MARINELINK.COM 37MR #1 (34-41).indd 37MR #1 (34-41).indd 371/2/2013 3:13:24 PM1/2/2013 3:13:24 PM