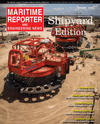
Page 19: of Maritime Reporter Magazine (August 2013)
Shipyard Edition
Read this page in Pdf, Flash or Html5 edition of August 2013 Maritime Reporter Magazine
www.marinelink.com 19maintenance tasks. The critical safety systems and hardware, however, must remain on the top of the list of mainte-nance items and not be overlooked dur- ing these difÞ cult times. The Þ ve year load testing and recerti-Þ cation process will effectively take a tired old marine off-load hook and re- new it to a hook that is like new and is safe and Þ t for its intended duty. The re- newal process begins with a preliminary dye penetration test to check for hidden cracks. The hook is then completely torn down and all parts are thoroughly inspected for damage or excessive wear. Following the tear down, the hook body undergoes a three step cleaning process including a degreasing, bead blasting and vibra-polishing using a ceramic bead medium. Other major components such as the locking pin, latch, positive lock components and mounting and as-sembly bolts are degreased and cleaned by hand. The hook is then rebuilt to factory speciÞ cations. When the hook is rebuilt, the locking pin spring, latch spring, rollers, pull cable, positive lock bushings, nylock nuts, cotter pins and all instructional label plates are replaced automatically with new OEM parts. After the hook has been reassembled, it is mounted on a purpose-built test Þ x-ture for load testing. The load testing for the Cranston Ea-gle hooks is a critical process undertak-en by an engineering team of the high-est caliber. Delta P Subsea Systems, Inc. works in partnership with Delta T Systems and is responsible for the load-testing portion of the hook renewal pro-cess. David Dupont, VP of Engineering for Delta P Subsea Systems, is in charge of the load testing process. The load that each hook will be pull tested to is equal to 2.2 times the safe working load (SWL) rating of the hook. Each load test is witnessed and signed off by a DNV or other class society of Þ -cial. Following the load test, the release tension for the pull cable is tested to en-sure that the force, which is required to open the hook, falls within the accept-able range as per the manufacturer?s speciÞ cations. Upon completion of the load testing, the hook will undergo the second dye penetration test by a certiÞ ed techni- cian. The dye penetration test is criti- cal for exposing any cracks or faults in the critical load path components of the hook that are not able to be seen by the naked eye. The hook is then shipped back to the vessel along with a full certiÞ cation report and is ready to be installed on the vessel for another Þ ve years of service.This ?call to action? is for the respon-sible party for each vessel that utilizes marine off-load hooks to inspect their hooks immediately to make sure that they are within their Þ ve year certi Þ ca-tion window and in good working order. The stakes are far too high to overlook this critical piece of load-bearing hard-ware.Michael Gabriel is director of the testing and certiÞ ca- tion program for Eagle Prod- uctsÕ hooks. In January of 2011, Delta T Systems, Inc. located in Riviera Beach, Fla., took on the role of the U.S. agent for Cranston Eagle (DBA Eagle Products Ky), a Finland-based manufacturer of off-load marine hooks. MR #8 (18-25).indd 19MR #8 (18-25).indd 198/1/2013 9:15:58 AM8/1/2013 9:15:58 AM