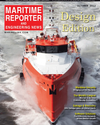
Page 20: of Maritime Reporter Magazine (October 2013)
Marine Design & Construction
Read this page in Pdf, Flash or Html5 edition of October 2013 Maritime Reporter Magazine
20 Maritime Reporter & Engineering News ? OCTOBER 2013 SAFETYA Shift in Culture is one of those terms that is used a lot in the maritime industry. We all think it is important, and every operator wants a ?good? safety culture. But how does one get it, and then keep it once it is there? This is the Þ rst of a pair of articles look- ing at safety culture in the maritime in-dustry. What is Safety Culture? The IMO tells us ?An organization with a ?safety culture? is one that gives appropriate priority to safety ... The key to achieving that safety culture is in:? Recognizing that accidents are pre- ventable through following cor- rect procedure and established best practice,? Constantly thinking about safety; and? Seeking continuous improvement.? This is a fair, but arguably limited de- scription. Safety culture is not something that a vessel operator either has or does not have. All operators have a company culture, and their culture (whatever form it takes) impacts safety of operations. All aspects of a company?s culture are relat- ed. It is very difÞ cult, if not impossible, to have an excellent and effective safety culture but a poor culture (for example) in terms of workplace cleanliness, em-ployee communication or employee engagement. The question therefore is whether the company culture enables, promotes and rewards safe acts. Safety Culture Basics The necessary components of a quality safety culture include the following.? Management LeadershipIt is generally agreed that safety must start at the top. In fact, some organiza-tional culture experts go so far as to say that ?... the only real thing of importance that leaders do is to create and manage culture? (Organizational Culture and Leadership, Schien, 2004). Manage-ment must view safety as a long-term investment in their company, not a cost. It is their role to consistently and visibly inspire and enable a culture of safety. It is also their role to be safety culture champions, to identify other champions, and to steward the process of cultural transformation. This usually means go- ing well beyond compliance and always means considering safety as a part of all decisions while allocating sufÞ cient re- sources to safety considerations. Build-ing an effective safety culture is not a switch that can be ?turned on,? but rath-er a sea change, or broad transformation that takes time to nurture. It takes time to implement the necessary changes, and even more time for employees to be con-vinced that this is a real, lasting change and not a fad soon to be abandoned. This management commitment takes real effort, but pays incredible dividends. Without strong, consistent and long-term leadership from the top, it is not possible to improve the quality of an organiza- tion?s safety culture. ? Training Clearly, safe operations require that all operational personnel are competent, understand and are skilled in safe proce-dures, and are aware of potential hazards AND how to avoid them. This is the job of initial and ongoing training. Atten- tion to training not only guarantees the above, but it also sends a strong message that management values safety and, con-sequently, values its employees. An em- ployee who feels valued and values him or herself is one who will do the right thing - even when no one is looking. Fortunately, we are in a time of great opportunity for implementation of new, effective and visible training programs. If training is not already top-notch at an organization then it can be made so using a breadth of new educational con-tent and techniques. And while a large budget never hurts, it does not have to be expensive. Given the importance of training, the beneÞ ts of investing in it, and the visible nature of its effects, at- tention to training is almost universally considered to be a necessary component of safety culture transformation.? Measurement and Continuous ImprovementAs I have written several times in earli-er articles, ?If you don?t measure it, you can?t manage it?. A high quality safety culture is one that requires measurement of safety performance. It uses those mea-surements as markers (key performance indicators or KPIs) to inform a process of continuous improvement. Without a system of measurement there is no way to learn from mistakes, nor any way to celebrate or build on successes. Mea-surements (and ongoing communica-tion of those measurements) are a key form of employee communication and a powerful demonstration of management leadership in the area of safety. ? A Focus on Learning, Not Blame Every day there are ?close calls? or ?near misses? that represent incredible learning opportunities. An accident is a very expensive way to learn a lesson. A close call is a practically free way - but only if the close call is reported, analyzed, turned into a learning oppor- tunity, and made public. The problem, of course, is that near-misses are almost never reported, especially in the absence of more than a few witnesses, because those at fault fear repercussions. The way around this problem is to have a policy ensuring that employees are not punished for an honest mistake or error in judgement resulting in an accident or near miss. At British Columbia Ferries Inc. (BC Ferries) this policy, as part of their huge cultural shift, has created an environment where an employee has no reason to conceal a near miss. This has yielded thousands of documented learn-ing opportunities through their so-called ?A.L.E.R.T? (All Learning Events Re-ported Today) incident reporting pro- cess. At the same time serious injuries have been reduced by two-thirds and continue to decrease. After speaking with front-line BC Ferries employees, it is fair to say that many view document-ing their own near-misses as a point of pride; knowing the report will help avoid a future accident, injury or even fatality. The key to this success is that employees trust (highlighted because this is a very important word here) that the company is going to adhere to the ?just? culture they have set up in terms of blame. This trust is powerful and takes time to build - but it is ultimately possible for any com-pany. ? Continuous Reß ection and Focus on Safety CultureAlthough somewhat covered above, this is worthy of its own mention. Safety and safe procedures must always top of mind for the entire organization. This means measurement and continuous im-provement, as well as a focus on learn-ing - both mentioned above. But it also means highly visible, meaningful and continuous evidence of commitment. One example that helps demonstrate company commitment to safety is regu-lar visitation from top-level manage-ment (preferably the CEO) discussing the company?s actions around safety, providing evidence on safety KPIs and Murray Goldberg is CEO of Marine Learning Systems. An eLearning re- searcher and LMS developer, his software has been used by 14 million people world-wide.t: 352-692-5493www.MarineLS.com ?A quality safety culture means doing things safely even when no one is looking? ?Safety Culture? MR #10 (18-25).indd 20MR #10 (18-25).indd 2010/2/2013 3:47:56 PM10/2/2013 3:47:56 PM