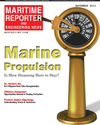
Page 66: of Maritime Reporter Magazine (November 2013)
Marine Propulsion Annual
Read this page in Pdf, Flash or Html5 edition of November 2013 Maritime Reporter Magazine
66 Maritime Reporter & Engineering News ? NOVEMBER 2013 Training & Educationthings up faster, and others may take a little longer to get certi Þ ed? Some need a little extra guid- ance. That?s why they come to the school. I don?t hesitate to grab my weld- ing gear and give them a demonstration of what I expect of them.So a welder here at BAE Systems Ship Repair doesn?t specialize as an alumi-num-only welder, or a steel welder. They?re going to learn how to weld steel and aluminum. The more certiÞ cations you have the more ß exible you are. If we feel you?re capable of re-ceiving a certiÞ cation, we go ahead and try to give it to you. Some have a harder time grasping a concept, so we let them work with what they have and try for additional certiÞ cations at a later time. Aluminum takes more skill and patience than standard steel certiÞ cations. Why is aluminum harder? The testing is much stricter. For example, when they conduct NDT?nondestructive testing?they put dye penetrate on it and if it bleeds through, then it?s a bad weld. Steel is not as strict. Some ships have superstructure made out of aluminum, and with all the twist-ing and turning from the ship, that soft material cracks easily. Aluminum is a lightweight, soft, low strength metal. Every time you get a ship in here it?s going to have some aluminum cracking. The processes we use to weld aluminum gives you a highly concentrated heat zone to prevent distortion.As a craftsman, what?s the difference between welding steel and welding aluminum? With steel, you can weld, clean it and get your supervisor to do a visual test and you can walk away. Aluminum is a completely different material; and it?s inspected to a higher standard than steel. It has to be good, sound metal; look good; be clean; and stand up to the non-destructive testing process. It?s just not getting a visual inspection, they?re actually conducting test. With 5XXX aluminum, every weld pass has to be checked by a QA inspector, which takes more time to Þ nish the job. If it is not done properly, it will show. Basically, there is no way to cover up bad welding with aluminum. Do you use robotic welding? We have machines?called Moggies?in the shop that we were test-ing and getting certiÞ ed on to weld dif-ferent material in different positions. We have an aluminum Moggy for our big in-serts. The way it works is you set it up, set the temperature and put it on track and instead of someone sitting there tak-ing three days to weld it by hand; you can take a few hours and get the job done right and in less time.Do you still need a certiÞ ed welder to set that up? You have to be certi Þ ed. We go through the whole process of checking every layer as if it was on the ship as a critical weld in a controlled environment passing the non-destructive testing. The yard itself is certiÞ ed and we do have certiÞ ed mechanics. So that would be something that you would do in a fabrication shop before you bring it over to the ship. Yes. We have a fabrication shop in the yard where we put together a lot of big pieces then take them to the ship to be installed.What do you Þ nd to be the most chal-lenging part of teaching welding? The different people . Every- one has different personalities, and they learn at a different rate. What one person may get, others may not, so you have to spend more time with them. Sometimes an apprentice does not understand a par- ticular certiÞ cation and I have to skip over that procedure with them. I research different ways of explaining and teach- ing different processes. I don?t know it all and I have to do my own research. So if I have a person that?s struggling on one thing and I feel that I?m not getting through to them, then I will try to Þ nd a different way to show them that they may grasp. What do you Þ nd most gratifying about teaching apprentices? When they get it after I have shown them different ways of approach-ing it. When they pass the test, they smile and feel good about themselves?it?s like a kid at Christmas. I feel good because I helped them do something that they are proud of. I feel like I?ve had a good day if I helped at least one person.What do you see for you in the future? I?m not sure. I?ve already been over in the ofÞ ce, but I wasn?t ready to get away from the shop. I wasn?t ready to leave welding. I still go on the ships regularly and might come back over the green line, you never know. But for now, I?m happy where I?m at. Welding is my passion. If I?m not welding, I would like to help someone else learn how to weld. Do you see a greater in ß ux of women getting into the program? As far as welding goes, I have seen it grow in the apprenticeship pro-gram. We?ve gone from one to two fe- males, and now we have Þ ve. I see it continuing to grow. They say females make better welders, anyway. We have a steady hand.I think over the years people think of welding as a man?s job, but people are now realizing that it?s a profes- sion, a trade that anyone can aspire to. So what would you say to somebody who was thinking about becoming a tradesperson, perhaps in the ship re- pair, ship building industry? Do your research. Look into it and make sure that?s what you want to do, especially working in the shipyard. You?re outside working in the elements. You might get wet, and maybe you can?t weld that day. You?re producing heat, and maybe it?s already 90 degrees out there. So you have to be prepared for it. Some people think about welding equals money. That?s all good and Þ ne, but you have to like what you?re doing Þ rst; you have to want to learn; and you have to get good at it so you can make money. You have to have that passion. You have to get into it.Is welding something that virtually anyone can learn, or do you need to have an aptitude for it? If you asked me this a couple years ago, I would have said anybody can weld. When I was an apprentice, and would go out on the boat, and all around me were guys that could weld; who had passed the test; and had the experience. But now, as an apprentice instructor and seeing students come in straight from high school, or maybe different compa- nies where they did more book work and not so much hands on welding, I see now that it?s not for everyone. Do you ever sometimes think about what you would be doing if you hadn?t become an apprentice here? I would probably be looking in the paper for a job, seeing who is paying the most. I don?t know. I do know I?m glad I am here at BAE Systems at this point in my career. I would not want to be anywhere else right now. ?Welding is my passion. If I?m not welding, I would like to help someone else learn how to weld.?MR #11 (66-73).indd 66MR #11 (66-73).indd 6611/11/2013 12:25:34 PM11/11/2013 12:25:34 PM