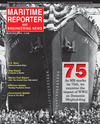
Page 29: of Maritime Reporter Magazine (January 2014)
Ship Repair & Conversion Edition
Read this page in Pdf, Flash or Html5 edition of January 2014 Maritime Reporter Magazine
www.marinelink.com 29
The Austal USA facility in Mobile, Alabama, is a state-of-the-art ship production facility, sporting a new dual line Module Manufacturing Facility (not pictured) which is as close to assembly line production as you can get in the maritime industry. al maritime exercises during her deploy- ment to Southeast Asia. USS Fort Worth has completed her scheduled mainte- nance period and is currently in her San
Diego homeport. Detroit (LCS 7), Little
Rock (LCS 9) and Sioux City (LCS 11) are in various stages of construction at
MMC. Wichita (LCS 13) and Billings (LCS 15) are in the early stages of mate- rial procurement.
If you hopped in your vehicle and drove 1,184 due south (this is not simply writer hyperbole: Marinette, Wis., lies at 87.6306 degrees West; Mobile, Ala., lies at 88.0431 degrees West) you would fi nd yourself at the second production facility for the Littoral Combat Ship pro- gram, Austal USA in Mobile, Alabama.
Austal USA builds the Independence variant of the LCS, an aluminum con- struction trimaran that measures 417 ft. with long with a 14.8 ft. draft. It, too, is able to exceed 40 knots, able to launch and recover watercraft in conditions up to Sea State 4; launch and recover air- craft in conditions up to Sea State 5. The
Independence variant features a massive mission bay with a volume of 11,000 m, and a range of more than 3,500 nautical miles.
Last month Austal launched the future
USS Jackson (LCS 6), unique in that it was the fi rst ship built in Austal’s new 59,000-sq. ft. assembly hall, Bay 5. The launch was conducted in a multi-step process involving Berard Transporta- tion’s self-propelled modular transport- ers (SPMTs) to lift the entire 1,600-met- ric-ton ship almost three feet in the air and moving it 400 feet onto a moored deck barge. The deck barge was then towed a half mile down river to BAE
Systems’ Southeast Shipyard where it was transferred to BAE’s fl oating dry dock, the Drydock Alabama. The fl oat- ing dry dock was submerged with Jack- son entering the water for the fi rst time.
Jackson was then towed back to Austal
USA’s facility, where it will undergo fi - nal outfi tting and activation before sea trials and delivery to the Navy.
This vessel is the fi rst of ten 127-meter
Independence-variant LCS class ships
Austal has been contracted to build for the U.S. Navy as prime contractor subse- quent to a $3.5 billion block buy in 2010.
Austal’s teaming partner, General Dy- namics Advanced Information Systems (a business unit of General Dynamics) is the ship systems integrator, responsible for the design, integration and testing of the navigation systems, C4I, and aviation systems. The ship’s fl exible open archi- tecture computing infrastructure (OPEN
CI), designed, developed, and integrated by General Dynamics Advanced Infor- mation Systems, allows “plug and play” integration of both the core systems and the LCS mission modules.
The LCS program is in full swing at
Austal USA with four ships currently under construction. Coronado (LCS 4), delivered to the Navy in September, will sail away soon with a commissioning ceremony in Coronado, Cal. in April.
Montgomery (LCS 8) is being assembled in Bay 4 in preparation for launch in the spring. Construction is well underway in
Austal’s Module Manufacturing Facil- ity (MMF) on Gabrielle Giffords (LCS 10) and Omaha (LCS 12). Fabrication on Manchester (LCS 14) is scheduled to begin in early 2014.
The Yards
While the Littoral Combat Ships them- selves are testaments to advances in marine technology and modern, fl exible weaponry and performance packages, a peak behind the scene at the shipyards tells the real tale, as both Marinette
Marine and Austal USA have invested mightily to deliver what are arguably the most modern and effi cient ship produc- tion facilities in the country.
Austal USA set up shop in Mobile,
Ala., in 1998, initially with a single ship- building shed. The evolution of the yard, particularly through the eyes of someone who saw it fi rst at start-up and then not again until late 2013, is nothing short of stunning. More than a decade and $300m in investment later, the ship construction facility in Mobile has evolved into a true vessel construction production line, where every piece of material, every piece of equipment, every ship module is well choreographed to minimize un- necessary time and handling, resulting in a straight path from design to delivery.
While the shipyard is vast, still grow- ing and impressive, the centerpiece is the
Module Manufacturing Facility (MMF) which sports two side-by-side manufac- turing lanes, a straight path linear, highly automated workfl ow which takes in ma- terial from one end and from the sides, moving it down the manufacturing lanes on rolling jigs and producing fi nished modules on the other end. The aim of the facility is simple enough: improve qual- ity and reduce costs. “It’s simple; it makes sense … but it’s something that no one has ever done,” said William C. Pfi ster, Vice President,
Strategic Facilities Development, Austal
USA.
While both lanes could be used for the same ship, today Austal uses one lane for the LCS program, the other for the
Navy’s Joint High Speed Vessel (JHSV) program. (Photo: Austal / US Navy)
MR #1 (26-31).indd 29 1/7/2014 10:42:13 AM