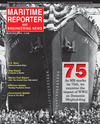
Page 34: of Maritime Reporter Magazine (January 2014)
Ship Repair & Conversion Edition
Read this page in Pdf, Flash or Html5 edition of January 2014 Maritime Reporter Magazine
34 Maritime Reporter & Engineering News • JANUARY 2014 & Cox Vice President, Business & Strat- egy Development.
A Revolution in Design
Getting all the shipyards on the same page would create effi ciencies, speed and economies across the board. It would make it possible to get identical parts and components from a broader ar- ray of manufacturers, who in turn could make fewer products to supply more customers – no customization necessary.
It would be nothing short of revolution- ary.
Up until about 1940, explains Tallant, most ships were custom-built, one at a time, in a single yard, using a set of plans that left many profi table details up to the imagination of the individual boat yard. To mass produce a large num- ber of ships, there needed to be a huge paradigm shift. Gibbs & Cox made ev- ery component on the ship well-defi ned and interchangeable, according to Mike
Schneider, a retired Navy captain, Proj- ect Liberty Ship member and SS John W.
Brown volunteer.
But the starting point for that transfor- mation was the blueprints themselves, “which meant you had to change the entire design process,” said Tallant. Ev- ery design fi rm had their own blueprint symbols, for example, which led Gibbs & Cox to create a common set of sym- bols covering not just all the parts of a ship, but extending to purchase orders, graphs, charts, reports and statistics. “At the peak of the war, we were pushing out 10,000 blueprints a month and almost 6,700 purchase orders a day. It was a huge amount of paperwork.”
Standardization enabled centraliza- tion of the procurement process, and streamlining the paperwork made it eas- ier to keep track of, order, and allocate constantly in short supply materials and parts, which could be routed away from a ship still under construction to one almost ready for launch when the need arose. These changes – probably one of the earliest examples of just-in-time manufacturing - along with the intro- duction of modular construction, are the foundation of cost-effective shipbuild- ing today, notes Tallant. “And this was all done by phone call or letter, before the advent of computers or the internet,’’ marvels Schneider.
The latter is where “Hurry up Henry”
Kaiser came in. He set up his shipyards as assembly plants where thousands of components preassembled at other fac- tories were fi nally laid in place. He set up training schools onsite to teach un- skilled laborers and switched from riv- eting to welding, creating Wendy the
Welder. Changes like this were said to have reduced man-hours by a third, cut ships costs from $2 million to under $1.7 million, and advanced ship construction into the next century. On average, it took 592,000 man-hours and 6,850 tons of steel to build a Liberty Ship.
Modern Shipbuilding
The most revolutionary change of all was the decision to go full bore to pre- fabrication and assembly lines. The Lib- erty was comprised of some 250,000 parts, a portion of which would come preassembled – i.e. the bow and parts of the deck house, bridge, double-bottom sections, stern-frame assemblies and bow units. Some estimates claim there was 43 miles of welding, 5 miles of wir- ing ad 7 miles of piping in each ship.
Taking this modern factory approach demonstrably shrunk construction time from the 10-12 months required in 1917 to 244 days at the start of WWII to an unheard of average of 30-42 days by the peak. Some Kaiser shipyards could do it in 2 weeks. By war’s end, as many as three Liberties a day were being launched. Drilling down into the actual physical construction, a decision was made to go to welded hulls, which required less skill, and a third less la- bor. “You can lay a line of soder much faster than someone can heat the rivet through,” says Horodysky. It also saved on metal as plates were now butted in- stead of overlapped, and that saved on weight, adds Schneider. The aggressive oversight of the commercial merchant fl eet, combined with standardization and revolutionary techniques, paid off. By the end of the war, the Maritime Com- mission had succeeded in running the most productive shipbuilding effort in history. From 1941 to 1945, the U.S. in- creased its shipbuilding capacity by more than 1,200%, producing 5,777 merchant and naval ships - a feat unmatched since.
A few lessons were learned along the way – some the hard way.
First, the Liberty design was tweaked to improve on the British predecessor.
Changes included: • Moving to a single, mid-ship house to accommodate the crew, which re- duced piping and heating needs. • Replacing three Scotch coal boilers with two water tube boilers. • Reshaping the hull into more of a straight line to better support mass production to cut down on the need for furnaceing to shape plates.
MR’S 75TH ANNIVERSARY
SS John W. Brown Liberty ship steaming down Chesapeake Bay en route port visits in Georgia and Florida in May 2002. (Cr edit: Pr oject Liber ty Ship)
The Liberty Ships
From Stem to Stern
Displacement: ..................................14,245 tons
DWT: ......................................................10,800
Length: ............................................441 ft. 6 in.
Beam: .........................................56 ft. 10.75 in.
Draft: ............................................27 ft. 9.25 in.
Propulsion: Two oil fi red boilers, triple expansion reciprocating steam engine, single screw, 2500 horsepower, fuel consumption of 26 tons a day.
Speed: ..................................................11 knots
Range: .....................11,000 miles or 20,000 nmi ......................................(37,000 km; 23,000 mi)
Complement: .......38–62 merchant marine sailors .................................21–40 Naval armed guards
Armament: Stern-mounted 4 in (102 mm) deck gun, variety of anti-aircraft armament
Capacity: ...........................................9,140 tons
Five holds could carry over 9,000 tons of cargo, plus airplanes, tanks, and locomotives lashed to its deck. A Liberty could carry 2,840 jeeps, 440 tanks, or 230 million rounds of ri? e ammunition.
MR #1 (32-41).indd 34 1/7/2014 10:50:28 AM