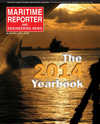
Page 10: of Maritime Reporter Magazine (June 2014)
Annual World Yearbook
Read this page in Pdf, Flash or Html5 edition of June 2014 Maritime Reporter Magazine
10 Maritime Reporter & Engineering News • JUNE 2014
TECH
Simplifying Float Over
Versatile
Ballast System
Mammoet recently introduced its
Versatile Ballast System, something it says is an improved ballast system that simplifi es and combines ballasting for load-out and fl oat-over operations. It is a sophisticated, yet simple, fully modular- ized system that is easily installed and fi ts any barge without the need for modi- fi cations. The system uses one equip- ment set-up that is able to perform both ballasting operations. This signifi cantly shortens the period for installation and decommissioning of the system on the barge, ultimately saving on barge rental time. Depending on other fl oat-over preparations, it can accelerate the installation time to get the platform in production up to one week earlier. The
Versatile Ballast System eliminates the need to convert the ballast system after load-out. This time-saving can speed up the platform production date by up to one week (depending on other fl oat- over preparations). It can be installed within two weeks, using a minimum of equipment, manpower and space. The main part of the installation can be performed on the quayside. This can save up to fi ve weeks of barge rental time. Decommissioning of the system is also faster; adding a further two – three weeks of time-savings.
OFFSHORE
A n offshore installation method that is more than three decades old is generating renewed inter- est from many operators who are chal- lenged with designing heavy-lift crane installations. Float-over installation has become a cost-effective alternative to lift installation for offshore construc- tion, as ever-increasing size and weight of decks constantly exceed the lifting capacity of ? oating cranes.
Exploration of oil and gas in more remote offshore ? elds is driving the increasing demand for larger offshore units along with ? oat-over installations.
In the coming four years, an estimated 660 offshore production platforms are expected to be constructed worldwide of which 180 weigh more than 12,000 tons.
Dockwise has a track record trans- porting and installing 15 topsides and with ? ve in the backlog. The SHWE topside installation in 2012 was one of the world’s largest and heaviest topsides transported to date, weighting 30,000 tons (including the deck support frame–
DSF) and transported for more than 4,000 nautical miles over a period of 23 days.
Float-over Strengths
Float-over installations have innate bene? ts due to the installation approach.
One of the key strengths of the ? oat-over is the lack of rendezvous risk, which is the schedule risk resulting from the need to have the crane and vessel in the ? eld at the same time. In principle, ? oat-over installations do not have a weight limi- tation as today’s heavy transport ves- sels (HTVs) are capable to transport and install mega sized topsides. In ad- dition, integrated platform installation eliminates extensive offshore hook-up and commissioning resulting in limited overall offshore exposure.
Float-over Phases
There are several phases involved when installing a deck with a semisub- mersible HTV. The ? rst is the standby phase where the HTV is at a safe dis- tance from the jacket but connected to the mooring system. Last minute ar- rangements such as preparing the ves- sel’s ballast system or the hydraulic jacks are under way.
The second is the docking phase where the vessel carefully enters the jacket slot, the distance between the jacket legs. Winches or tugs are used to pull the HTV carefully into position.
In the third phase, pre-mating, the vessel positions the deck directly above the jacket. Once positioned, the HTV ballasts to match the leg mating unit (LMU) with the receptors on top of the jacket legs. During this phase, it is criti- cal that the vessel motions be limited to suit the chosen LMU geometry. No weight transfer yet occurs.
For a successful ? oat-over operation, countless hours of preparation come down to the exact moment when the deck makes contact with the jacket. The fourth phase is the most critical point of the installation leaving no room for un- certainty in the functionality of the load transferring equipment.
In the mating phase, the deck is low- ered onto the jacket by the vessel’s rapid ballasting system where large quantities of water enter the ballast tanks, which enable the HTV to submerge. During this phase, the deck’s weight is com- pletely transferred from the vessel onto the jacket. Custom engineered elasto- mer is used in the design of the LMUs to dampen the friction during load transfer.
In the post-mating phase, the deck sits secure on top of the jacket and a gap is created between the deck support unit (DSU) and the HTV to ensure vessel motions will not cause contact between the two.
In the exit phase, the vessel departs from the jacket slot on its own propul- sion or with assistance from tugs. These ? ve phases may slightly differ depend- ing on equipment and installation ap- proach.
Float-over Requirements
There are three essential speci? cations required for an HTV to perform a ? oat- over. The ? rst is the HTV’s width being the right size. The vessel must be narrow enough to ? t inside the jacket slot. Sec- ondly, the vessel must be designed with an open stern and equipped with mov- able casings. The open stern enables the
HTV to exit the jacket slot during the last phase of an installation. To ensure the deck is perfectly positioned onboard the vessel, casings, which facilitate bal- ance and ballasting, can be moved to best accommodate the cargo. Lastly,
HTVs must have suf? cient strength and stability to carry and transport heavy decks.
Offshore Float Over Installation 30,000 TONS, 4,000 NAUTICAL MILES, 23 DAYS
Bigger and heavier decks are on the horizon, in- stalled in more remote locations.
Image: Mammoet
MR #6 (10-17).indd 10 5/28/2014 11:43:47 AM