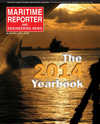
Page 69: of Maritime Reporter Magazine (June 2014)
Annual World Yearbook
Read this page in Pdf, Flash or Html5 edition of June 2014 Maritime Reporter Magazine
www.marinelink.com 69 can’t have any leaks in them.”
For more than 70 years, the lines have remained leak-free. According to
Schneider, there is no known record of any maintenance being performed on the ballast lines. The grooved couplings vis- ible on the piping today are the original couplings installed in 1942. In more than 70 years of service, the couplings never leaked or required replacement.
The Details
Found on the grooved carbon steel pip- ing of the ballast system are ? exible mal- leable iron Victaulic couplings, which at the time were referred to as standard couplings for grooved steel pipe. Victau- lic Style 77 ? exible grooved couplings are the equivalent of these couplings to- day.
Lines from the engine room to the forepeak tank, the bilge wells in the for- ward three cargo holds, and the #1 and #2 cargo deep tanks are joined with the couplings. The four lines to the deep tanks are 4-inch diameter lines and have around 32 couplings. These cargo deep tanks and the associated piping are not in use today, but were designed to handle cargo oil carried in the tanks. The single line to the forepeak tank is a 3.5-inch di- ameter line and has approximately nine couplings. This line is still in use and carries fresh water stored in the forepeak tank.
The four lines to the bilge wells in the #1 and #2 cargo holds are 3 inches in di- ameter and are for pumping water from the bilge wells. There are approximately 18 couplings on these four lines. All numbers are estimates because not all couplings are presently exposed.
The Bene? ts
From ease and speed of installation to accommodation of piping system move- ment and vibration, many of the reasons grooved couplings were likely selected for the John W. Brown are the same rea- sons grooved systems are speci? ed for new ship construction, retro? t and repair today.
Because Liberty ships needed to be constructed quickly—Bethlehem-Fair- ? eld could build one in as few as 28 days and launched an average of almost two each week—speed and ease of installa- tion was probably the most important factor in selecting grooved joining sys- tems for the Brown. Simply put, grooved mechanical piping systems help yards build, commission, test and turn over ships quicker.
A grooved joint comprises four ele- ments: grooved-end pipe, a gasket, coupling housing, and nuts and bolts.
The groove is made by cold form- ing or machining a groove into the end of a pipe. A gasket is centered around two abutted grooved pipe ends, and the coupling housing segments are placed over the gasket so that the key sections of the housing engage the grooves.
The bolts and nuts are tightened with a socket wrench or impact wrench. In the installed state, the coupling hous- ing encases the gasket and engages the grooves around the circumference of the pipe to create a leak-tight seal in a self- restrained pipe joint. Following installa- tion, the joint can be visually inspected: metal-to-metal bolt pad contact con? rms proper assembly.
With no heat or ? ame required for as- sembly, grooved systems offer easier, safer installation than welded systems.
The lack of welding reduces or elimi- nates fumes and particulate matter emis- sions, hot works, ? re watches and the con? ned space considerations and other precautions speci? c to welding. Com- pared to ? anges, grooved couplings offer considerable weight and space savings.
The ? exibility and vibration attenua- tion qualities of grooved couplings like- ly helped increase the life of the Brown’s ballast system piping. Flexible grooved couplings permit a limited amount of linear and angular movement at the pipe joint, which can accommodate system expansion and contraction and help ab- sorb the strains and stresses imposed on the piping as a result of typical ship operating conditions. This ? exibility can also accommodate minor misalign- ment, which would have simpli? ed the assembly of large prefabricated sections of the Brown and the coordinating pip- ing systems within each section. Exces- sive vibration can decrease the lifetime of a piping system, but the elastomeric gasket contained within the grooved coupling creates discontinuity, reducing noise and vibration transmitted through the piping.
The longevity of the John W. Brown and its ballast system demonstrate the advantages grooved piping systems can bring to the shipbuilding industry. Many of the qualities considered in pipe-join- ing systems 70 years ago still hold true today: speed and ease of installation and maintenance, safety, reduced ? re haz- ards and issues associated with welding, reduced downtime, and reduction in vi- bration and noise transmission. Liberty ships were at one point referred to as “? ve-year ships” for their expected ser- vice life, but the Brown has proven that a well-maintained vessel with durable, reliable piping systems—the veins and arteries of a ship—can greatly exceed expectations.
Project Liberty Ship
Project Liberty Ship is dedicated to the preservation of the Liberty ship S.S.
John W. Brown as a living memorial to the men and women who built the great
Liberty Fleet and to the merchant sea- men and U.S. Navy Armed Guard who sailed the ships across the oceans of the world. Project Liberty Ship offers public tours, educational programs and Living
History Cruises aboard the Brown. This “Voyage into History” is an exciting six-hour ride during which guests learn about the ship’s history through histori- cal reenactments, live music, ? ybys of vintage World War II aircraft and tours of the museum spaces, crew quarters, bridge, ? ying bridge, chart room, radio room, mess rooms, troop berthing areas, stern gun deck and more.
Visit www.liberty-ship.com for hours of operation, to purchase tickets and to learn more about the history of the vessel and volunteer opportunities.
Ship Location: Pier One, 2000
South Clinton Street, Baltimore, MD
Phone: 410-558-0646
Ballast lines onboard John W. Brown
About the Author
David Gibbons is Maritime Division Man- ager with Victaulic, a leading producer of mechanical pipe-joining and fi re protec- tion systems. Victaulic develops prod- ucts for a full range of industrial, com- mercial and institutional applications.
For more information, visit www.victau- lic.com.
MR #6 (66-74).indd 69 6/9/2014 11:33:47 AM