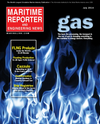
Page 56: of Maritime Reporter Magazine (July 2014)
Offshore Energy Structures & Systems
Read this page in Pdf, Flash or Html5 edition of July 2014 Maritime Reporter Magazine
56 Maritime Reporter & Engineering News • JULY 2014
The recent trend in favoring newer gen- eration engines which offer improved fuel consumption by using a longer stroke re- fl ects the marine industry’s focus on en- ergy effi ciency. While this design does aid operators in reducing fuel consump- tion, it has also created the new issue of cold corrosion. The longer stroke allows the cylinder walls to cool more than with older engine designs, allowing water con- densation to form on the surface which then reacts with the sulphur dioxide in the combustion gases to form sulphuric acid, a corrosive element which damages the liner surface. The iron compounds formed by this process are then fl ushed into the cylinder oil, leading to excessive wear of the cylinder liner with the cost of a replacement at an average cost of up to $150,000.
To benefi t from the more fuel-effi cient engines without creating a related is- sue that could potentially cause damage to costly engine parts, operators need to carry out effective and accurate condi- tion monitoring. In recent service let- ters, MAN Diesel & Turbo has reiter- ated the importance of monitoring of the conditions within the cylinder chamber in order to minimize the effects of cold corrosion. Having conducted extensive research into the issue, Parker Kittiwake have concluded that identifying the level of damaging corrosive elements within the cylinder chamber and understanding the processes which lead to these levels building up is the most effective way of preventing wear. Frequent testing pro- vides ship owners with a comprehensive overview of conditions within the cylin- der chamber, allowing operators to avoid costly repair bills by addressing harmful levels of corrosive elements before they cause damage.
To obtain an indication of the level of corrosion within the cylinder operators can measure the concentration of iron compounds in used cylinder oil. Once the underlying causes have been identifi ed and understood they can be eradicated or limited, preventing cold corrosion from causing damage. Most commonly available monitoring tests indicate the total iron fi gure in the cylinder oil, in- cluding both metallic and non-metallic compounds. These elements have differ- ing properties and are caused by distinct processes. Iron particles worn from the cylinder liner by cat fi nes are metallic and can be detected by onboard ferro-analyzer tests. However, non-metallic compounds such as iron sulphate are caused by re- actions in the cylinder liner during the combustion process, and these cannot be detected magnetically. In order to identify the causes of corrosion ship owners need to monitor the levels of both metallic and non-metallic elements separately so that preventative measures can be taken.
With accurate information key to pre- venting corrosion, shipowners need in- formation. While there are onboard test- ing solutions available, these often take several hours to complete and do not pro- vide separate data for the level of metallic and non-metallic iron compounds in the sample.
The recently launched Parker Kittiwake
Cold Corrosion Test Kit is designed to give the most comprehensive analysis of corrosive elements in cylinder lubricants, providing a measurement of non-ferrous iron compounds present in a sample al- most instantly, negating the need to send samples to a laboratory for analysis and avoiding the time and cost this incurs.
By having quick and simple access to this information onboard, operators can identify where adjustments need to be made to alter the operating conditions within the cylinder in order to minimize corrosive wear and reduce cost. The test kit, when used in conjunction with ferro- magnetic analyzers, will indicate the lev- els of both metallic and non-metallic iron compounds so that operators can isolate and address the different processes which result in these corrosive elements being formed. As the issue of cold corrosion increasingly gains recognition, OEMs are looking to identify ways to minimize the effects and prevent damage. As a result many OEMs are now advocating the use of higher Base Number (BN) lubricants in engines with a longer stroke, MAN Die- sel & Turbo now recommend lubricants with a BN of 100 or higher, and so it be- comes more important to monitor the cyl- inder oil to understand the effects of this change on the conditions within the cylin- der chamber. Scrape down oil is continu- ally exposed to acidic combustion prod- ucts that need to be neutralised before they corrode engine parts. By frequently testing the residual BN of used cylinder lubricant, operators can ensure that al- kaline reserve levels within the oil are suffi cient to neutralize these acidic prod- ucts, preventing unnecessary corrosive damage. Parker has recently updated the
Digi TBN Test Kit which measures the residual BN levels in used cylinder oil, providing an onboard fi gure in minutes.
This allows operators to monitor the ef- fi ciency of cylinder lubricants over a long period of time, maximizing the potential life of the product as well as saving both the time and cost incurred with repairs re- sulting from corrosive damage.
Innovative engine technologies offer at- tractive benefi ts to ship owners by simul- taneously addressing two of the greatest challenges facing today’s shipping indus- try; fuel reduction and emissions control.
With immediate access to the necessary data through onboard condition monitor- ing tests, they are better armed against cold corrosion and can reap the benefi ts of eco-effi ciency, minus the unwelcome consequences.
Combat Cold Corrossion via Condition Monitoring
PRODUCT FEATURE: MONITORING TOOLS
Parker Kittiwake explains why frequent condition monitoring is the most effective measure in combating the recent cold corrosion phenomenon
Cold Corrosion Test Kit
MR #7 (50-58).indd 56 6/30/2014 11:11:49 AM