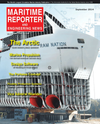
Page 42: of Maritime Reporter Magazine (September 2014)
Marine Propulsion Edition
Read this page in Pdf, Flash or Html5 edition of September 2014 Maritime Reporter Magazine
42 Maritime Reporter & Engineering News • SEPTEMBER 2014
MR 75TH ANNIVERSARY obviously - think three-dimensional (3D) and virtual reality - but more im- portant, the design process has changed as well
FORAN today is an integrated CAD/
CAM/CAE system that can be used in the design, production and manufac- ture of ships. Subsystems run the gamut from hull structure to machinery, to outfi tting, electrical and drafting and mechanical designs. “Expert add-ons” include a PLM link, virtual reality and
Control Management. All information is stored in an Oracle database. Among other changes, the most recent version enables the visualization of the ship 3D model already generated in FORAN into a virtual reality environment, two areas Sener and it’s competitors see as key to the future.
The Windows-based system compris- es several application packages, a num- ber of common modules (build strategy, 2D drafting, 3D walk-through design review, concurrent engineering), links with production equipment, interfaces to management systems and an integrat- ed development environment. There are two major lines of business: the design of ships and marine structures, and the development of FORAN, its design and construction software that now boasts worldwide commercial success.
Key to FORAN’s endurance, believes de Góngora, is its ability to provide a single solution from the fi rst stage of the design to the complete assembly and delivery of ship, without requiring the assistance of any third-party software.
While the company doesn’t provide product lifecycle (PLM) management, it does provide a link to those products. “We are the only one who can provide a single solution,” de Góngora claims.
The transformation of the industry, meanwhile, during FORAN’s expansive lifespan, has been “dramatic,” resulting in measureable benefi ts, according to de
Góngora. “One benefi t is time. This is very important in the ship building in- dustry. We have shorter delivery times compared with 25 years ago, because the time required to build, assign and construct is much shorter.”
This, despite the added complexity in ships being designed today. Even in the face of more complex ships, CAD de- sign packages help ship builders to con- tinue to win the race for shorter delivery times. More complex operations of the ship require more complex technology.
And that complexity in a product, says
Aveva’s Neuveglise, helps drive the need for more 3D. For example, the more equipment in a given space, the more you need to be able to see in 3D to be able to navigate the area, and the ear- lier in the process the modeling is done, the better. “Doing more in the same space of time is actually an advance,” says SSI
CEO Darrell Larkins, adding that to- day, it’s not so much about being able to do the same thing more effi ciently, but rather, about the ability to do more. Put another way, he said, “Software might let you do something a thousand times faster when what you are really trying to accomplish is 1,000 times more com- plex.”
On top of the savings in time, ship- yards can achieve a signifi cant reduc- tion in materials waste and cost because design software enables accurate fab- rication information and in essence, guarantees no interferences. Scrap from construction of parts is then reduced to minimum.
So what kind of ROI are we talking about? “If you are in a shipyard that is not highly tech-oriented, you could see savings of 30% to 50%. If you take into account a state-of –the-art shipyard, the improvement is less. We are speaking about 10% in worst cases. But this is something. Ten percent in the price of a ship is many millions of U.S. dollars,” says Sener’s de Góngora.
Another way to tackle waste and push consistency is to enable information about modifi cations and the data col- lected in the PLM system to be sent back up the information chain into the computer-aided process planning (CAPP) system from the PLM package, something Sener and Aveva are work- ing on. “If you are building more ships of one class, the second ship is almost equal.
The third and fourth are not the same – some modifi cations will have been made.” Transferring those changes back down the line will enable those modifi - cations to be made to subsequent ships far more easily, notes de Góngora.
Sharing that data more quickly, “I guarantee there will be more consis- tency between the phases of design than before,” said Neuveglise
This is where Aveva touts the benefi ts of adopting the concept of lean manu- facturing from the auto industry. In- vented by the founder of Toyota, lean manufacturing is about how to be more effi cient in production. It is based on no waste, respect of everyone and their job, and a continual feedback loop at all lev- els. It’s the concept of providing feed- back from production back to the design stage that really intrigues Aveva. “Sometimes when doing a detailed design, you fi nd something that is not easy to do, or which needs to be further fabricated. So production tells the guys in basic design, ‘Don’t do that anymore for future reference,’ ” says Neuveglise.
It’s even more important in shipbuilding because unlike automobile manufactur- ing, which is designed and built sequen- tially, in ship building, it’s all done at the same time, which makes the process much more complex. “So if something is discovered in the detailed design phase, you need to tell the folks in basic design, and until recently, we weren’t able to have this kind of feedback,” he adds.
That will change in the next genera- tion of ship design processes as soft- ware will need to address two issues, in de Góngora’s view: • Collaborative design on a global level. “The ship building industry is a paradigm of globalization,” he says, noting that the design, various parts of the ship, the basic ship, the owners and suppliers typically are spread out around the world. “We need to keep working on a collaborative solution for “If you are in a shipyard that is not highly tech-oriented, you could see savings of 30% to 50%. If you take into account a state-of –the-art shipyard, the improvement is less. We are speak- ing about 10% in worst cases. But this is something. Ten percent in the price of a ship is many millions of U.S. dol- lars.”
Rafael de Góngora, GM, Sener
Design software can do more than eliminate a task here and there. It can signifi cantly reduce the required number of crew, saving a substantial amount of money over the life of the vessel.
Alain Houard, VP, Marine & Offshore
Industry, Dassault Systèmes, maker of Catia design software and 3D and simulation applications.
MR #9 (40-49).indd 42 9/4/2014 10:49:10 AM