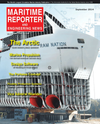
Page 57: of Maritime Reporter Magazine (September 2014)
Marine Propulsion Edition
Read this page in Pdf, Flash or Html5 edition of September 2014 Maritime Reporter Magazine
independent of each other on the same ship, and as a result, that was making it really hard for us to get our avails done well. And so now we’re integrating those much better. Doing maintenance and modernization requires good solid planning and contracting. We will con- tinue to have to balance how much mod- ernization we can afford, but the life- cycle maintenance has got to be done.”
Hilarides says that as NAVSEA and the
Navy strive to institute a culture of judi- ciousness and affordability, commonal- ity is part of that equation. “Why do we have 247,000 types of valves on ships? If there’s a valve we repair every quarter, that valve should be common across every ship in the fl eet so that we get the economies of scale for production and repair. If that valve nev- er gets repaired in the 35 years of a ship’s life but once, commonality doesn’t mat- ter. We’ll pay that one-time cost to go do that repair. We work on air conditioning plants all the time and we have a LOT of different air conditioning plants on all our ships. So they’re a perfect target for a commonality initiative,” he says. “We can get economies in acquisition, train- ing, repair and operations.”
Hilarides has created a new position on his staff, the director of acquisition and commonality. “We’ve stood up a direc- torate, and they’re on the trail of some really good things, including fi nding ex- amples where we have one spec for pro- duction of a valve that gets interpreted by ten different organizations, both in- side my life lines and out, such that the valve manufacturer produces 10 differ- ent packages, paperwork packages, to go with the valve he manufactures exactly the same way. There’s savings in that.
So we’re going after that. I think Rear
Adm. Tom Kearney and his team are off on the right track.”
Balancing Capability & Affordability
Affordability is directly related to requirements, and managing risk, Hi- larides says. “In our culture of afford- ability, we have good, hard requirements discussions with the Pentagon. Over the years, I’ve looked at requirements and acquisition as a partnership. There are checks and balances in that. Not every requirement is a good requirement. With early requirements, changes are very easy, while late requirements have to be a very high standard,” he says. “We have to go make sure we’re having the right conversation with our requirements authorities—of which there are many— to make sure we have the right cost and capability balance for what we deliver.” “When we talk through the require- ments, we have to look at the cost,” Hi- larides says. “If you have to be able to make 8 knots with moderate battle dam- age, there’s a couple of ways you can do it. You can take the propulsion train— the diesels, shafts, and the screws— and put them into that full MILSPEC hard- ened, no-matter-what-you-do-to-‘em, they’ll still work. Or, you go build an armored box in the front, far away from the rest of the propulsion system, with an 8-knot outboard motor that you can lower down after that damage event, and still meet the 8-knot requirement. We’ve spent a lot of time on that. It really makes people uncomfortable; they’re like, “Whoa! You put the propulsion train on a commercial standard? It’s still very survivable, because commercial ship operators don’t want their ships to fail if they hit the bottom or get hit hard by a tug. Still fairly good, but you invest in protecting the emergency gear. That’s the conversation that’s going on: which parts of the ship do you not want to get destroyed by a missile? The magazines; command and control structures; your well deck so that you can continue to get the Marines off or back on in that 8-knot transit out there?” “It’s actually probably the best ship de- sign discussion we’ve had in a very long time, inside the government,” he says. “When we decided to take LCS 1 and 2 and deliver them as ships of the fl eet long before the design was mature, we actually intended them to be engineering development models, to go learn, and get them wet,’ so that we design the right class of ships in the long term. Once we owned them, we chose to deploy the fi rst ship early,” he says. “There’s some risk in that. If it were an airplane, you wouldn’t deploy EDM airplanes. We deployed an EDM ship. It did a pretty good job. It met the fl eet commander’s need for ships out in that part of the world, and did a good job of showing the
US fl ag. But it had some problems, and we seemed to have spent a lot of time apologizing about that. Well, we did exactly what we said we would do. We took the ship, pushed it to the front as fast as possible, and learned a lot.”
By comparison, Hilarides points to the
Virginia-class submarine. “We took sev- en years of requirements trades; seven years of design; and seven years of con- struction to get the fi rst ship out. When it went to sea it was in pretty good shape.
But Hawaii and Missouri were much improved compared to the fi rst two, Vir- ginia and Texas.” “With LCS, we chose to accelerate that process. We took just a couple years of design; went to production early – we took a lot of risk there; and deployed early,” Hilarides says. “Until you sail it all the way across the Pacifi c Ocean, you don’t really know how it will work.
We tried a new maintenance model out in Singapore, and learned a lot, and as a result of that, follow-on ships will be better and better, and the learning curve is much accelerated from what it would have been under a traditional process. “We take some risk to provide excep- tional ships at an affordable price, and we don’t always hit the mark,” he says. “But that’s not to say we shouldn’t take any risk in our new developments. So getting that balance right is important.”
Why do we have 247,000 types of valves on ships?
If there’s a valve we repair every quarter, that valve should be com- mon across every ship in the fl eet so that we get the economies of scale for production and repair. www.marinelink.com 57
MR #9 (50-57).indd 57 9/3/2014 10:53:33 AM