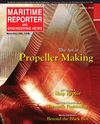
Page 46: of Maritime Reporter Magazine (January 2015)
Ship Repair & Conversion Edition
Read this page in Pdf, Flash or Html5 edition of January 2015 Maritime Reporter Magazine
MARINE PROPULSION 1,100 degree Celsius liquid bronze is ? owing into the prepared propeller mould.
Particularly sensitive areas, the leading and trailing edge, are sharpened by hand.
technique which is dif? cult to replicate. a new territory for him to ? ght for new most the East-German Shipyards. One tured here for the former DDR-? eet. In
This leads to the point that Japan, Korea customers. “After the fall of the wall our of the big ? nancial scandals after the 1991 the partly modernized Mecklen- and China could not form large competi- employees would not want to be part of German reuni? cation followed: The burger Metallguß GmbH (MMG) was tion for manufacturing propellers “Made the old management any longer,” Urban Vulkan-bosses took hundreds of mil- founded; 170 people worked there in in Germany” … so far. “Our experience said. lions Deutsche Mark of subsidy pay- 1992, and sales were around $8.8 mil- from more than 50 years are not that But when Urban took the helm, he ments for their western companies – but lion.
easy to copy,” said Urban bluntly. barely had a chance. went bankrupt in 1995 and this in? u- The ? nal breakthrough and build-out
It also can become very expensive if The former State DDR built vessels enced also MMG. towards the worldwide leading manu- a propeller of a giant container ship or exclusively for the Soviet Union – for A second privatization followed. facturer of giant ship propellers was tanker – or for that matter any commer- rubles, which were almost instantly enforced by the acquisition of Deutsche cial vessel – breaks during normal op- without value in the West. Regardless, The Path Forward Gießerei- and Industrie-Holding AG eration, as lost time is lost money, and in practically overnight the company lost “Engineering in ‘Waren an der Müritz’ (Dihag) in 1999. In the beginning of many of today’s markets that is a com- its only large existing customer. has a more than 135-year tradition,” said 2008 about $32 million we invested into modity that many ship owners can ill af- But the problems did not end after the Urban. The “Maschinenbauanstalt mit the production facilities to be “ready for ford to lose. privatization. Eisengießerei” was founded in 1875, the future.”
When he engineering graduate Urban MMG was sold in 1992 by the trust which has been changed into “Eisenwerk Up to today the company has invested took over the management of the com- company (Treuhandgesellschaft) to Waren” in 1913. Since 1948 the ? rst big- about $82.9 million to create what it pany after the ‘fall of the wall,’ it was Bremer Vulkan, which has taken over ger ships propeller have been manufac- dubs the largest and most modern pro- peller factory world-wide.
The Art of Making Propeller
Making propellers to drive ships at sea is a liberal mix of art, science and expe- rience. The mix of the material is not a secret, as about 80 percent is copper with the remaining 20 percent consisting of aluminum, iron, manganese and nickel.
The true art of propeller making comes in the design, casting and mechanical post-processing, and unlike many man- ufacturing entities in 2015, the lowest price is certainly not the most appealing virtue for owners that are serious about running ef? cient ships.
But what is it that makes a medium- sized company from the Mecklenburg province a world market leader for big ship propellers? “Well,” said Urban a bit reserved, there are certainly a “few tips and tricks.”
But the real reason in addition to tech- nological intuition and optimal quality, is “the con? dence” which customers put into MMG. “Ship builders must rely on us to re- ceive on-time what they expect,” said
Urban. This con? dence in MMG has been increased continuously during the 46 Maritime Reporter & Engineering News • JANUARY 2015
MR #1 (42-49).indd 46 MR #1 (42-49).indd 46 1/7/2015 10:57:58 AM1/7/2015 10:57:58 AM