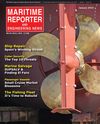
Page 52: of Maritime Reporter Magazine (January 2016)
Ship Repair & Conversion Edition
Read this page in Pdf, Flash or Html5 edition of January 2016 Maritime Reporter Magazine
PROPULSION UPDATE
Composite Materials for
Bearing Bonding to Secure Rudder Integrity he critical requirement with rud- depending on the ? nish of the housing and pintle liners. Due to their excellent during assembly will need to be removed der bearings relates to the bush and the size of the bearing. However, the durability, high compressive and adhe- immediately.
Figure 2: Slip method
Tretention in the housing. Because pressing requires a large force, propor- sive strength, low moisture absorption the bush is manufactured from a differ- tionate with the size of the bearing, and and electrical insulation characteristics, ent metal to the bearing block, local gal- can damage a bearing that is not in line composite materials are ideal for the vanic corrosion can occur, which causes when ? tting. stable installation and permanent bond- the housing to become oversized until The freeze ? tting or shrink ? tting tech- ing of rudder bushes. Isolating the bear- eventually the bush can no longer be nique can be used as an alternative meth- ing into position, Belzona resins and held in the correct alignment. This mis- od. The two methods of freezing using paste grade composites provide a 100% alignment can result in the development liquid nitrogen are full immersion and contact between the bush and the hous- of annular gaps between the housing and vapor freezing. In full immersion, the ing, ensuring a permanent vibration-free the bearing bush, resulting in excessive bearing is placed in a container which location and eliminating galvanic and and premature bearing wear, a malfunc- is then ? lled with liquid nitrogen until crevice corrosion. tioning rudder and, consequently, costly reduction of the bearing to the required
Picture 2: Bearing housing installed repairs and loss of sea time. diameter. Once the required diameter using composite materials
Due to a combination of severe vibra- has been achieved, it can be removed tion, constant fretting and an aerated sea from the nitrogen and will then be held water environment, bearing installation in place in the housing until the bearing can be a real challenge. The ideal instal- returns to its original size. However, this lation would provide a perfect seal be- method is very slow and time consuming tween the bush and the housing while because it takes a long time to reduce the offering a complete corrosion protection. bearing diameter and to generate enough clearance for ? tting. The vapor freezing
Figure 1: Rudder bearing structure can also be used to ? t the bearing by va- porising liquid nitrogen directly within the bearing until reduction. It will then be placed in the housing until returns to its original size. This method is more Application Methods of
Composite Materials b) Injection Method cost effective and safer than the immer-
Belzona recommends two techniques
Bearing bonding can be carried out by sion method but the rate of bearing con- for bearing installation with composite injecting the material between the bear- traction is a lot lower.
Using the same concept, another ? tting materials: the slip method and injection ing and the housing. The Belzona shim method. When installing the bearing, takes up any ovality or housing wear, technique consists in heating the hous- ing in order to expand it. This technique special attention should be given to the thus creating a durable barrier with involves hot work and can incur health method used to align and centralise the 100% surface contact, electrically isolat- ing the bearing. This method has been and safety issues and thus requires an bearing bush within the damaged hous- assessment of the risks before carrying ing. The techniques described below can
Picture 1: corroded housing Figure 3: Injection procedure be used to rebuild, realign and electri- out, which can be highly time consum- cally isolate many types of bearing bush ing. While these methods are very ef- fective, there will be limitations in the housings, including: • Rudder bush housings level of corrosion protection they pro- vide. Indeed, the bush and the housing • Internal stern tube, bush housings are made of dissimilar material and they • A-frame bracket bush housings • Stabilizer in shaft bearing will remain in direct contact, causing the problem of local galvanic corrosion to bush housings reoccur. All the processes will require • Oversized cutlass bearing housings accurate machining of housing and/or a) Slip method bush to ensure clearances are within tol-
The slip method consists of simply erance for installation.
Traditional Techniques sliding the bearing into the housing. A
When replacing rudder bearings on ? lm of composite material is applied existing boats it is dif? cult to match Composite Chocking to the prepared inside surface of the the inside and outside dimensions of Composite chocking offers an alterna- the old bearing. The three conventional tive to traditional press and freeze ? tting housing and also to the outside surface techniques of ? tting rudder bearings are that ensures not only accurate alignment of the bush. Further material is applied press ? tting, freeze ? tting and heating but also long-term secure location of the in excess to the internal surface of the housing to prevent air entrapment after bearing. Nowadays, polymeric com- the housing. posites and coatings are widely used assembly. The bush is then jacked into
The ? rst technique, press ? tting, con- sists of pressing the bearing into the in the marine industry for the reseating position in the housing and correctly housing. The ease of ? tting will vary or installation of new rudder bearings aligned. Any excess material extrudes 52 Maritime Reporter & Engineering News • JANUARY 2016
MR #1 (50-57).indd 52 1/10/2016 11:03:31 PM