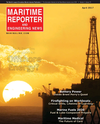
Page 45: of Maritime Reporter Magazine (April 2017)
The Offshore Annual
Read this page in Pdf, Flash or Html5 edition of April 2017 Maritime Reporter Magazine
detailed CAD model of a topsides module. Using this models used in wind tunnel and wave basin testing and complex 3D Rhino model using the surface wrapper high-? delity CFD model, HydrOcean investigated the the numerical CFD model. in STAR-CCM+, which shrink-wraps a high-quality effects of multiple wind angles on the platform, match- Traditionally, in physical experiments used to assess triangulated surface onto the geometry, closing holes, ing experimental data from wind tunnel and wave ba- wind loads over offshore structures, the detailed CAD joining disconnected and overlapping surfaces, as well sin tests with wind generation capabilities to within 10 model of the platform is simpli? ed substantially in the as automatically discarding obsolete surfaces. The gen- percent - and in most cases 3 to 5 percent - at a fraction process of creating a physical model for testing. Small erated grids in this model had on average 140 million of the cost. pipes are replaced by porosity grids, while com-
The project was ? nanced through Collaborative & In- plex objects are replaced by boxes, cylinders or novative Technology Program in Exploration and Pro- other simpli? ed geometry. But in this project, duction of Hydrocarbons (CITEPH), a French national the participants realized that contemporary 3D program that facilitates access to private funding of in- printing technology would make it feasible to novative R&D projects in oil and gas and related en- produce physical models that reproduce all the ergy industries (http://www.citeph.fr/en/). This was the details contained in the CAD model. Mean- second of two CITEPH projects in which HydrOcean while, for numerical simulation, in theory, any received funding from Total to develop and validate the kind of geometry can be captured with today’s use of numerical CFD technology, speci? cally STAR- CFD meshing tools.
CCM+, to compute wind loads on offshore platforms. Hence, in this project, there were two paral- lel workgroups. On the experimental side were
CITEPH Wind Loads I CSTB, a provider of research, testing, certi? -
In the CITEPH Wind Loads I project, completed in cation and training for built-environment and 2013 and funded entirely by Total, HydrOcean used construction industries which managed wind
CFD to reproduce results of wind tunnel experiments tunnel testing for the project, and OCEANIDE, that had been performed for a large FPSO unit in West an offshore and coastal engineering ? rm that
Africa. The project successfully validated the use of took charge of wind load experiments in wave
CFD for such applications, and enabled to identify the basin testing.
bias of experiments such as con? nement, scale effects Meanwhile, on the numerical side of the proj- and boundary layer effects. ect, HydrOcean’s goal was to take a 3D CAD model of the platform topsides provided by
CITEPH Wind Loads II DORIS Engineering designed for other pur-
With the use of CFD validated, the CITEPH Wind poses (layout, MTO) and mesh it directly with-
Loads II project was designed to push CFD to its limits. out having to suppress or correct any geometry
This project, again managed by HydrOcean, required details. After months of trial and error, Hy- ? nding ways to increase the ? delity of both the physical drOcean succeeded in meshing this extremely
FIGURE 1:
Views of the full-featured CFD model.
FIGURE 2:
Flow simulation results using full-featured CFD model.
www.marinelink.com 45
MR #4 (42-49).indd 45 MR #4 (42-49).indd 45 4/4/2017 1:34:13 PM4/4/2017 1:34:13 PM