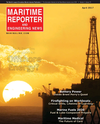
Page 47: of Maritime Reporter Magazine (April 2017)
The Offshore Annual
Read this page in Pdf, Flash or Html5 edition of April 2017 Maritime Reporter Magazine
FIGURE 4: Correlation of CFD simulation versus physical test results (dots show simulation results, dashed line shows test results).
Key Players
Key individuals leading the project for their respective organizations were Alain Ledoux, naval architect at Total S.A., Olivier Langeard, proj- ect engineer at DORIS Engineer- ing, Daniel Barcarolo, PhD, Senior
Aero & Hydrodynamic and Project engineer at HydrOcean, Graham
Knapp R&D engineer at CSTB,
Benjamin Rousse Chief Scientist at Océanide and Olivier Bachman, support and application engineer at Siemens PLM.
the CAD model - is nonetheless much ping setting and methodology. Initially, the wrapper, so it explored how to adjust parameter settings that yielded simula- more straightforward than the labor-in- the solution did not converge. Upon the wrapping process to create a volume tion results that in all instances were tensive geometry simpli? cation and de- closer examination, HydrOcean found mesh that would yield a simulation that within 10 percent of experimental values. featuring traditionally required for CFD the simulation model showed some areas converged. Over some 15 iterations, Thus, HydrOcean delivered an industri- model preparation. Their goal, says Hy- of very high pressure, high velocity pro- numerous surface parameters were var- ally feasible CFD simulation approach drOcean, was to develop a comparable ? les and other results that revealed some ied, seeking to ? nd the best connection for full-scale, high ? delity, fully featured approach for CFD. regions of the volume mesh were not of among elements while avoiding such offshore platform modeling with STAR-
The 3D CAD model that HydrOcean high quality. things as suboptimal triangulation areas CCM+, which will lower prototype and received from DORIS Engineering in Those results, it says, were caused by in the mesh. In the end, it found surface testing costs in the industry.
Rhino format was a clean and for other purposes other than CFD modeling (lay- out, MTO, etc). However, it presented some features that such as multiple dis- connected surfaces and elements, and very high levels of geometric detail which made it dif? cult to mesh for a
CFD analysis.
Initially, the Siemens PLM support team suggested that HydrOcean split the model into multiple boxed regions, per- form a local wrapping of each box, then perform a single wrapping operation to merge all the boxes. But HydrOcean decided that approach would require an unrealistic amount of time and labor and would not be the industrially feasible method sought by Total and DORIS.
Instead, HydrOcean decided to invest considerable time and research in ? nd- ing how to apply the surface wrapper tool to accomplish meshing of the entire geometry in a single process, without splitting the geometry and signi? cant loss of detail. The majority of time was spent on ? nding how to create a wrapped surface that could generate a very good volume mesh.
The quality of the simulation solution, as con? rmed by comparison with experi- mental data, will be the con? rmation that
HydrOcean had found a very good wrap- www.marinelink.com 47
MR #4 (42-49).indd 47 MR #4 (42-49).indd 47 4/7/2017 3:00:31 PM4/7/2017 3:00:31 PM