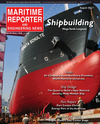
Page 65: of Maritime Reporter Magazine (August 2017)
The Shipyard Edition
Read this page in Pdf, Flash or Html5 edition of August 2017 Maritime Reporter Magazine
Figure 1 he layout of ship propellers is a balancing act between opti- mal power conversion and the
Tavoidance of unwanted cavi- tation effects, which can result in dam- age to the propeller structure and higher noise levels. MAN Diesel & Turbo in
Frederikshavn, Denmark, is using the computational ? uid dynamics (CFD) simulation solution STAR-CCM+ from
Siemens PLM Software to model cavita- tion and optimize ship propellers.
Two mid-size container ships of 8,500
Image courtesy MAN Diesel & Turbo
TEU – CSCL Europe and CSCL Amer-
Figure 1: ica – will be upgraded by retro? tting a the CFD-based optimization of ship pro- shipyards with a wide range of engines,
In the non-homogeneous wake ? ow, ef? cient Kappel propeller. It is powered pellers as well as on related topics, in- as well as complete drive trains (engine, sheet cavitation occurs on the leading cluding simulations incorporating the ef- propeller, shaft, aftship energy-saving by a MAN 12-cylinder, two-stroke die- edge of the propeller in the upper re- fect of the wake, cavitation simulations device and propulsion control system) sel engine, which is capable of giving the gion due to increased angle of attack propeller shaft a power output of 68,520 including an estimation of the erosion in which the individual components are and low hydrostatic pressure. This be- risk, and the analysis of scaling effects. optimally designed to suit each other kW. comes detached (cloud cavitation) or
MAN Diesel & Turbo is a leading sup- and the speci? c application. The com-
These dimensions are even more im- becomes tip vortex cavitation.
pressive when one considers that the plier of drive components for various pany designs and manufactures propel- entire power output has to be converted types of ships. The company supplies lers with diameters of 4 to 12 meters and into propulsion as ef? ciently as possible by just a single propeller. Ship propellers
Cavitat on for drives of this size have a diameter of
Cavitat on is the format on and implosion of cavit es in liquids. It occurs when the hydrostat c pressure falls below the 10 meters or more, weigh over 100 tons evaporat on pressure of the liquid due to high ? ow velocit es. Vapor bubbles are formed, which are entrained by the and are manufactured with high preci- ? owing liquid into areas of higher pressure, where the vapor in the cavit es suddenly condenses and the vapor bubbles sion from special alloys, such as nickel- collapse. The ship propeller is considered one of the main sources of onboard noise and vibrat on and the correct determi- aluminum bronze or stainless steel al- nat on of cavitat on extension is crucial in securing the comfort of passengers and crews. Cavitat on on the surface of solid loys.
bodies can cause microscopic deformat on of the surface material due to the high mechanical stresses. Over t me, larger part cles break o? the surface. Di? erent types of cavitat on include sheet cavitat on, cloud cavitat on, t p vortex cavitat on,
Ship Propellers – a Balancing Act and supercavitat on.
The greatest challenge for designers of ship propellers is to use the available engine power as ef? ciently as possible in order to minimize fuel consumption and therefore operating costs: a mid-size container ship will consume bunker fuel at a rate of more than 100 tons per day.
At a cost more than $300 per ton, even marginal improvements in fuel economy will lead to signi? cant savings.
However, propeller designers do not have unlimited freedom, a propeller de- signed with too much emphasis on pow- er output can produce various cavitation effects, which can result in undesirable vibrations and noise levels and give rise to erosion of the propeller structure.
In addition, the propeller does not act within a nice homogeneous ? ow ? eld, but in the wake of the ship’s hull, and the propeller blade passes through various ? ow regions with different pressure and speed ratios during each rotation.
MAN Diesel & Turbo
Dr. Keun Woo Shin is a research en- gineer in the Propeller & Aft-Ship R&D department at MAN Diesel & Turbo in
Thrustmaster’s complete line of mechanical and hydraulic azimuthing thrusters are trusted
Frederikshavn, Denmark, and is very fa- sY?ŽwGŽIlSGwŽ?lEGwAYEsYOE?YAwsÐAuu?ÐŽ?sOŽYGESGA|?usOŽÐG?AOŽY??tslS?s?G??Ð miliar with this problem. As a member lŽ?DtAYEÐŽYIO??AOŽY?sYÐu?EsYO?YEG??AlG?wŽ?YlAduG??Gl?AÐlAduG?AYEŽ?ldŽA?E?
of the propeller R&D team, He has been dS???lwA?lG?SA?A?Žu?OŽYIŽ?G|G??SGA|?usOAÐÐusÐAOŽY?
working intensively for many years on ????dS???lwA?lG??YGl www.marinelink.com 65
MR #8 (58-65).indd 65 MR #8 (58-65).indd 65 8/7/2017 3:32:31 PM8/7/2017 3:32:31 PM