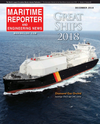
Page 13: of Maritime Reporter Magazine (December 2018)
Great Ships of 2018
Read this page in Pdf, Flash or Html5 edition of December 2018 Maritime Reporter Magazine
and costly environmental regulations and unpredictably into hard, empirical facts. tiguard® fusion technology which integrates silicone- consumer demand, the weight of responsibility can Six key stages comprise the SHAPE measuring and hydrogel and full diffusion control of biocides in a drag even the most robust shipping business backward. monitoring system. First, the vessel’s individual speed single coating. An innovation that can deliver a six per power reference curves are established. This is followed cent fuel savings across the entire docking interval and
A burden of responsibility by collecting in-service data which is then cleansed and a maximum speed loss of 1.4 per cent over ? ve years.
This is why proactively seeking opportunities to en- puri? ed to eliminate extreme operating conditions and With fuel costs set to increase for vessels burning low hance operational ef? ciencies, to reduce costs and build the effects of environmental factors. Next, a precise sulphur fuels from 2020, this amounts to a considerable long-term sustainability into the framework of every ves- speed loss calculation is performed. This is a critical reduction in fuel bills – and optimal ef? ciency in service sel is now a pre-requisite for every savvy shipping com- measure for understanding vessel performance and fuel delivery for customers who expect to receive what they pany. To operate at optimal ef? ciency, ship operators and ef? ciency as power increase and speed loss are directly want, when they want it, and exactly how they want it. managers need to be able to carefully monitor and control related. From this, the four KPIs are calculated: the fuelling requirements, energy consumption and oper- - Dry docking performance – calculates the ational performance of each vessel. This requires tangible changes in hull and propeller performance evidence of how a vessel operates against set criterion over drydocking periods.
or key performance indicators (KPI’s) and baseline mea- - In service performance – calculates the ef- surements for the vessel, which can be compared over fectiveness of the vessel’s hull and propeller time and in comparison, with its equivalent competition. solutions.
More so, the insight is gained by analysing how perfor- - Maintenance trigger – calculates the mance is improved or inhibited by control factors such as change in hull and propeller performance the operating environment or the application of perfor- over a given period between drydocking and mance enhancing technologies. With eco-ef? ciency tech- in-service use. nologies for commercial vessels – which are designed to - Maintenance effect – calculates the change improve performance and reduce costs – data is key. This in hull and propeller performance before and is very much the case with hull coating solutions. after a maintenance event.
Fouling can dramatically affect a ship’s hydrodynam- ics and the frictional resistance from the roughness Delivering optimal ef? ciency caused by slime on a ship’s hull can result in an in- Following this in-depth analysis, Hempel crease in fuel consumption. Shells, barnacles, oysters can offer solid, valuable technical advice to and mussels on the hull can lead to a huge drop of 18 the ship operator, advising them on the op- per cent in ef? ciency (on average over ? ve years), as erational decisions they can take to positively the ship burns more fuel just to maintain a given speed. impact their fuel ef? ciency and ensure best
This problem is exacerbated on vessels with unpredict- practice in vessel maintenance. This includes able trading patterns and longer idle periods. ensuring the right hull coatings are selected to
Using intelligent software and working closely with optimise particular aspects of vessel perfor- coatings experts, long-term trends can be monitored us- mance, in line with the trading requirements ing in-service KPI’s to develop and deliver an optimum of the particular vessel. This is very important, protective coatings solution for that vessel. Important- as not all hull coatings are created equal, nor ly, the empirical measurements that result can be uti- will they deliver the same ef? ciency gains. lised to showcase a vessel’s performance to customers, Hempel’s Hempaguard® range, for example, ? nanciers and other stakeholders; to show how a vessel is particularly suitable for vessels tasked with stacks up against its competition. This data intelligence moving regularly between warm and cooler is evidence of the latent ef? ciency savings to be made. waters, and those which routinely switch be- tween steaming at slow and regular speeds or
Tracking progress sit idle. Hempaguard is an innovative fouling
This is where Hempel, the global coatings manufac- defence product containing 95 per cent less turer’s, new hull performance system SHAPE (Systems biocide than traditional antifoulings, but still for Hull and Propeller Ef? ciency) comes in. The system offers outstanding resistance to fouling during is founded on the ISO 19030 framework which de? nes idle periods (of up to 120 days). Hempaguard a methodology to measure changes in hull and propeller retains its effectiveness when steaming at slow performance and details a set of relevant performance or at regular speeds; and when alongside in indicators for hull and propeller maintenance. This pro- port. This gives shipowners enhanced ? exibil- cess provides shipowners with extremely detailed and ity over their ? eet utilisation. accurate information on the performance of their ves- The product provides these bene? ts through sels – translating what is happening below the waterline Hempel’s patented innovative low friction Ac- www.marinelink.com 13
MR #12 (10-17).indd 13 MR #12 (10-17).indd 13 12/5/2018 4:23:02 PM12/5/2018 4:23:02 PM