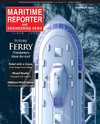
Page 47: of Maritime Reporter Magazine (February 2019)
Ferry Builders
Read this page in Pdf, Flash or Html5 edition of February 2019 Maritime Reporter Magazine
T
TECH FILE: HEAVY LIFTERS
Heavy Plate for Big Lifters
Heavy plate from Dillinger used in the world’s largest offshore heavy-lift cranes
In Liebherr’s Type MTC 78000 heavy-lift ofshore table, the central element of the crane. This supports for the welding work. Liebherr in Rostock machined all cranes, 2000 tons lifting capacity puts them among the two mast sections one above the other, the diameters these segments to a thickness of precisely 130 mm, in world’s largest machines of their type. When deployed of which taper from 8.5m at the bottom to 3.8m at the order to assure the necessary absolute fatness. on the world’s largest heavy-lift vessels such as the top. The crane can be rotated through 360 degrees even
OSA Goliath for drilling-rig modifcations in the Gulf when bearing its maximum load, since all machinery, the dimensions of Mexico, limits of the load-bearing capacities of both winches, etc., are installed above the slewing ring. The The welding together of the frst of the total of 12 the design and the materials are approached. base column, at 370 tons, the lower mast section, at 250 rings making up the mast was a very special highlight
In addition to their out-of-the-ordinary proper- tons, the upper mast section, at 160 tons, and the 89m for Karl Thrumann, project engineer at Liebherr in Ros- ties spectrum, including yield strengths of up to 690 long boom (311 tons) make up the crane’s dead-weight tock, who was the project manager responsible for the
MPa, the unique diversity of thicknesses and formats of 1790 tons. Compared to all this, the slewing ring, construction of the frst MTC 78000. of steels from Dillinger provided the decisive impulse with its “only” approximately 70 tons, is virtually a “It simply flls you with awe to see weights and di- for their use by Liebherr-MCCtec Rostock GmbH in fyweight. Even the quadruple hook on the main hoist mensions like these,” he recalls. the MTC 78000. These steels assure the cost-efcient weighs in at no less than 66 tons. Looking back, he refers to the privilege of tracking construction of this crane, and lasting dependability in Dillinger supplied a total of 1400 tons of DILLI- and guiding the construction of the MTC 78000 and its operational service far out at sea. A total of 1400 tons of MAX steels, of which 1200 tons took the form of high- subsequent installation on the OSA Goliath from start steel in thicknesses up to 200 mm are used in the MTC strength heavy plate with minimum yield strengths of to fnish as an experience unique in his professional 78000, 900 tons being high-strength steels in Z grade. 690 MPa, for the construction of the MTC 78000. In career. “It was an absolutely spot-on landing. Every-
The basis for these far-reaching projects is provided by addition, 900 tons of these high strength heavy plates thing ftted: an excellent performance from everyone, the perfect interaction between two industry leaders in were produced in conformity to the customer’s unique extremely good co-operation and, above all, satisfed quality and technology. specifcations. This order included 200 mm thick plates, customers.” by means of which the girder-mast boom was fastened He has now been involved in the completion of three
Heavyweight Stars at its rear end, no less than 10m wide, to the mast using other heavy-lift ofshore cranes of this type, all employ-
Installation vessels work at sea for several months only two bolts, both of 500 mm in diameter and 730 mm ing only German steel from Dillinger, as specifed by on end installing, modifying or dismantling ofshore long. Each of these bolts weighs 1.1 tons. The weight the customers. platforms, laying miles-long pipelines and setting up of the boom and the forces exerted by the load generate ofshore wind turbines. At lengths of 180m, beams of enormous stresses, which the steel used at this 32m and a 25812 t gross tonnage, the OSA Goliath and most critical point in the crane’s structure must her sister-ship, Sampson, are among the world’s largest continuously withstand. High-strength heavy heavy-lift vessels of this type. plates from Dillinger were also indispensable
A total of three cranes are used on board - the Lieb- for the fabrication of the slewing ring. These herr MTC 78000 heavy-lift crane, with its maximum plates transmit the enormous forces from the load of 2000 tons, and two others, with lifting capaci- mast into the hull of the vessel, generating ties of 100 and 70 tons, respectively. stresses acting in the plate-thickness direction.
Liebherr-Werk Nenzing GmbH developed the frst Welding of the slewing ring segments gave rise
MTC 78000 heavy-lift ofshore crane with a maximum to additional stresses, since the stif structure dynamic load torque of 78000 kNm for the OSA Goli- hinders shrinkage during cooling. The use of ath. It was then built and installed on the OSA Goliath Z grade heavy plates in thicknesses up to 145 at the Liebherr yard in Rostock. The crane can lift its mm and in sizes which only Dillinger can sup- maximum load of 2000 tons - equivalent to the take-of ply in this grade provided a solution that is weight of fve fully loaded Jumbo jets - with a reach of both cost-efective and reliable. Such plates up to 35m. Its lifting capacity within a radius of 74m are produced from high-strength steel contain- is up to 530 tons, and still no less than 500 tons at its ing only extremely small percentages of un- maximum reach of 87m. In addition to its main hoist, desirable impurities, such as sulfur. Cast into it also has two auxiliary units, with lifting capacities of slabs or ingots of a thickness unparalleled any- 200 and 50 tons. where in the world, this steel is homogenized
Despite its enormous size, the MTC 78000 is de- right down into its center by rolling it at roll- signed as a mast-type crane incorporating conventional ing forces of 11000 tons, and then additionally slewing-bearing technology, but with one inner and one water-quenched. The size of these plates made outer bearing on a single level. These slewing bearings it possible to fabricate the slewing ring, with are 9m in diameter, and are thus almost twice as large its diameter of 9.2m , from only four segments, as most other rolling-element bearings of this type. each weighing 35 tons. Time and cost-savings
They connect the 10m high base column to the turn- of up to 50 percent were reportedly achieved www.marinelink.com 47