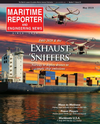
Page 79: of Maritime Reporter Magazine (May 2019)
Propulsion Annual - Green Marine Tech
Read this page in Pdf, Flash or Html5 edition of May 2019 Maritime Reporter Magazine
BWMS: Special Advertorial
How to Engineer a Reliable
Ballast Water Management System
By Pete Thompson, V.P. of Operations, Ecochlor
Electrical engineer performs FAT on the Ecochlor treatment system generators at the new ProFlow manufacturing factory in North Haven, Connecticut USA.
he ability of Ballast Water Management Systems (BWMSs) to operate reliably
Reliability is a Growing Concern with Shipowner/Operators over the lifetime of the vessel is not something that happens by accident. In
In March, the American Bureau of Shipping (ABS) released the 2019 Best Practices for
T fact, reliability comes down to the choices that engineers make when designing Operations of Ballast Water Management Systems Report, a culmination of feedback from and specifying a new BWMS. It’s no secret that minimizing equipment failure and shipowners and operators with installed BWMS who participated in three conferences maximizing long-life means using high quality components in the build and simplifying over a span of two years. The report is based on a survey, discussions and workshops the system operation so that there are fewer moving parts. that were used to review the “industry’s progress toward compliance and identi? ed best
However, creating a well-constructed BWMS that will operate trouble-free over the practices that supported successful BWMS installation and operation.” long term means additional production costs – costs that manufacturers must justify so
Through these channels, BWMS operational reliability was recognized as growing that shipowners fully understand the value of reliability against the very real risks and problem. Their concern was based on a history of system failures and the hardened costs associated with breakdowns and non-compliance.
stance of regulators in the enforcement of BWM compliance.
Some of the reliability issues addressed in the report were “the use of unreliable or non-
Build for the Life of the Vessel
OEM equipment or components (? lters, sensors, sampling pumps, valves, actuators, “When we consider equipment design, the ? rst criteria we look at is quality. We work electrolytic cell assemblies, dosing sub-systems, UV reactors, etc.).” with our supplier network and our customers so that we have the relevant operational
Other common problems included: “? uctuating and unstable TRO sensor and data to ensure that the equipment will hold up to our strict durability and endurance monitor readings that are sensitive to environmental conditions…; frequent outages standards,” says Leif Melhus, Ecochlor Engineering Manager. Melhus continues, “We and replacement of UV lamps and clogging of ? lters that require frequent or continuous make sure that our suppliers understand the ship operators’ requirements and the nature back-? ushing operations…; [the] inability to operate EC-based BWMS in freshwater or of the environment that the equipment must operate within. In this way we can ensure low salinity water conditions, requiring alternative arrangements to carry salt water or that our systems are ‘? t for purpose’ all the way down to the component level.” brine solutions…; and, predicting low UV transmittance challenges (affecting all UV- based BWMS) caused by weather (seasonal) or other variables… .”
Engineered Reliability
Overall, as summarized from 487 installations using seven BWMS treatment
This attention to detail has a downside in increased costs, with the ? nal system prices technologies on a variety of vessel types – 65% were either inoperable or had problematic potentially a little higher than the lowest market expectations. Melhus counters this by ballast operations and only 25% ballasted regularly with a testing protocol for ef? cacy adding, “While cost is a consideration, it is not the primary factor when we are choosing in place. components. This means that sometimes our production costs might be a bit more, but we know that our customers will see the bene? t of the choices we make through
Planning for Reliability increased reliability and the dependability of the Ecochlor BWMS to operate for years to
Reliability can be determined by looking at the time between equipment breakdowns come. This ‘engineered reliability’ ensures that our customers maintain compliance with and system operation. At a minimum, BWMS manufacturers should be able to reference the ballast discharge standards.” how many of their systems are operational at any given time. Ecochlor goes the extra
Unfortunately, not all BWMS manufacturers have followed this principle. Some mile with this thinking, using real-time data analysis to ensure that reliability and system systems have been built with cost rather than quality in mind, and whilst these might uptimes are maintained at the highest possible levels. have been the least expensive option in the market many ship operators have found out
Ecochlor Service Manager, Max Hasson said, “The ongoing monitoring of every the real costs when they turned them on. Not only did these systems not work, but in Ecochlor system that is installed on a vessel, wherever it is in the world, is an important some cases the manufacturer didn’t have the capacity to service the equipment to bring factor in helping us keep their system fully operational. The crew sends us operational it back on line. In other cases, the manufacturer has left the industry completely! It data after every ballast operation and that information is incorporated into a weekly has been a costly lesson for shipowners to replace these systems with more dependable internal ? eet update charting the vessel position, next port of call, last ballast operation, options.
chemical tank levels, operational concerns, requested parts, and a preventative “The Ecochlor system was built to last the life of the vessel,” shared Tom Perlich, maintenance schedule. We don’t sit back and wait for the next service call; we plan our
Ecochlor founder. In 2006, we retro? tted the Moku Pahu, a U.S. ? ag, Jones Act bulk way to increased reliability for the ship’s crew.” carrier with a route from Hawaii to San Francisco. With ballast operations in California, this vessel encountered some of the strictest regulations in the world. For 13 years this
Conclusion ship ran ballast operations using the original installed system until her last voyage in
There are many factors that come under consideration when engineering a BWMS
January of this year. As our longest continuously operated BWMS we enjoyed not only for longevity, durability and reliability. With ? nancial penalties, shipowner’s reputation, a highly collaborative relationship with the crew but also the ability to gather valuable port state detentions/barred entry or charter losses as consequences of BWM non- data on the system’s components over the years. That experience has been fed right back compliance, securing a reliable system is paramount to good business practices. into the systems that we deliver to customers today.”
Reliability costs money, but the unreliability of a BWMS will cost you even more.
MR #5 (74-81).indd 79 5/2/2019 11:36:18 AM