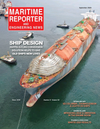
Page 40: of Maritime Reporter Magazine (September 2020)
Marine Design Annual
Read this page in Pdf, Flash or Html5 edition of September 2020 Maritime Reporter Magazine
HEAT & VIBRATION MITIGATION less steel and a stitched and woven insulation fabric that is unique solutions to address the need to manage heat and vi- designed to better withstand the pressures of heat, vibration bration. Recently Thermamax developed housings for battery and time. modules to support electri? cation, beside others, for marine
Over the years Thermamax has continued to invest in new application. Also, on board ships electri? cation is becoming machinery, for example laser cutting machines that today are more and more important. Thermamax battery housings can ? ve times more ef? cient than machines were 20 years ago, be used for on-board energy storage systems,. Thermamax but at the same price point. And the advent of CFD simulation battery housings ensure effective ? re protection and extend has allowed it to ensure that not only are its insulation solu- the battery range by balanced thermal management. But in re- tions optimized for heat and vibration characteristics, but that gard to market guidance, Cronauer it was still too soon to tell they are engineered for ease of assembly and maintenance by how fast and how far these newer applications would move.
unskilled workers; to maximize material use, “so maybe we At the end of the day, the company is able to lean on the don’t neet 2 mm thickness, maybe 1 mm is enough. And do multiple markets it serves. “From the automotive side you can we need 215 screws, or maybe only 120?” learn a lot of cost-ef? ciency, cost-engineering, secure pro-
Thermamax continually invests in R&D to test new materi- cessing,” said Cronauer. “From marine we learned a lot about als, but to date stainless steel and ? ber materials are still the combining multiple materials into a single function. This is a go-to. “There is some movement (at the R&D departments key factor in making Thermamax a leader in providing com- that manufacture insulation material), but there hasn’t been plex solutions.” a real breakthrough. For example, a cladding design without any ? bre material. From a physics perspecitve, it is possible The Tmax-Retro? t and it works perfectly on the test bench but the question is ... In the engine room temperatures are highest and reliable who will be the pioneer for this new design?” ? re prevention is vital. As 3D details are often not available
But manufacturing in the marine sector is a low-volume af- for older engines, retro? tting with SOLAS-compliant high- fair for all, and Cronauer stress the importance of a skilled performance insulation systems has only been possible to a workforce to deliver consistent quality. limited extent until now. With Tmax-Retro? t, older marine “Blue-collar workers in Germany go through an apprentice- engines can now also be upgraded with high-temperature in- ship program that is three years long, certi? cate-based and sulation systems which exceed SOLAS guidelines. The all-in- teaches them how to work skillfully with metal (and other one package provides all services – from the preparation of materials).” the engine’s 3D pro? le to the thermography of the developed
As the maritime market moves increasingly to news fuels, and installed insulation system – all from one source.
hybrids and batteries, Thermamax evolves too, engineering “We see retro? t opportunities, as there are many old ships
A 3D Scan
The Thermamax retro? t solution starts with a 3D scan of the engine.
Photo: Thermamax 40 Maritime Reporter & Engineering News • September 2020
MR #9 (34-49).indd 40 9/9/2020 8:51:03 AM