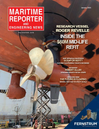
Page 16: of Maritime Reporter Magazine (January 2021)
The Ship Repair & Conversion Edition
Read this page in Pdf, Flash or Html5 edition of January 2021 Maritime Reporter Magazine
Back to the Drawing Board on the construction of the tug.
So there was a chance you could have been designing (In regards to autonomy), there certainly has been a lot of buildings instead of boats?
RA I recall saying to my father “Maybe I’ll just become media attention to autonomous vessels in the past decade, an architect instead of a naval architect.” And my father, who more media attention than perhaps attention (or interest) was a very wise man, said, “You could do that and become from owners. (That said), we have actively been working on one of tens of thousands of starving architects. Or you could autonomous vessels, and we have some projects that have stick with the marine side and get to be a big ? sh in a little progressed, but it is going to be a slow adoption process. pond.” And that turned out to be pretty prophetic. We see it (evolving) as ? rst remotely operated vessels, then semi-autonomous vessels. We’re focused primarily on areas and operations where autonomous vessel offers an obvious
When you look at how the company from where it started advantage, such as ? re? ghting, or on the other side, monoto- to today, how has it evolved?
RA Well, let’s start with the differences because there are nous, uncomfortable jobs crews. I don’t see autonomous ves- a lot easier to identify. We started out as a one-man operation sels replacing tugboats for typical operations anytime soon. working out of a basement of? ce; today we’ve evolved to a But what I would hope to see is, like we see in the automo- company of about 90 people with a global outreach. tive industry, integration of technologies that are being de-
The way we do business is totally different, evolving from veloped to allow autonomous operation into manned vessels, all manual drafting and manual calculations to a complete- to improve the safety and ability of crews to be a little more ly computerized, high-tech kind of operating environment. comfortable.
Probably one of the most invisible, but most important chang-
One non-technical challenge we regularly discuss is es, is how we work. Our work now is much more structured grooming the ‘next generation.’ How do you see it?
and detailed, working to ISO standards in how we document design work and design decisions. That makes record keep- RA There are so many interesting technical challenges to- ing for the future generations in? nitely easier. day that it’s an exciting time to be in (this business), and I see
What’s the same? Our subject matter has never really that continuing for at least the next generation. We’ve got 20 changed: a focus on purpose designed work boats. My grand- or 25 years before we’re all supposed to be carbon neutral, father, and I think particularly my father, set a tone for the and as Mike outlined, there are huge technical challenges to way in which we do business; working honestly, with integ- overcome (particularly in this smaller vessel category). rity, with strong relationships. That’s something that I hope MF When I was going to university in Australia, the naval will never change. architecture program was co-operated with the aeronautical engineering program. At the time there were about 60 stu- dents in the aeronautical program and six in the naval archi-
With decarbonization, digitalization and autonomy, I tecture one. On the job boards there were three jobs for aero- would contend that the maritime industry is in a nautical engineers and seven for naval architects. I ? gured transcendent period. What’s your opinion?
Mike Fitzpatrick Decarbonization is certainly at the fore- those were pretty good odds, and I think the same is probably front of many projects, and it presents probably the biggest still true today. challenge to the industry today, mainly because it’s dif? cult to
Nine decades is quite an achievement for any business make the economics of decarbonization work, particularly in today. When you look back, what do you consider your small workboats. The capital cost difference of a low carbon company’s greatest achievement?
tug boat for instance, is typically on the order of 30% more expensive than a typical diesel mechanical tug. We’ve done RA How much time did you say we have, Greg?! I’ve numerous LNG fueled tugs dual fuel tugs, hybrid tugs, and been immersed in the corporate history for the last year or they’ve pretty much all been done when there is some outside so, particularly in these COVID-isolated times. I think ? rst source providing (a ? nancial) incentive to have it done. and foremost, surviving for 90 years as a continuous business
Digitalization is certainly the one that’s made the big- is a pretty signi? cant achievement. And particularly when gest difference in how we do things. Look in the shipyards, one looks at starting a business at the beginning of the Great where in the past a typical shipyard might have spent 5,000 Depression, then surviving those “Dirty 30s” as a one-man hours working on the production level design, and then spent enterprise. I know that that was an extremely dif? cult and 100,000 hours building a tugboat. The more advanced and discouraging time for my grandfather, a talented, ambitious most ef? cient shipyards today spend 15,000 hours on a really and proud man. There was a couple of years in the early 30s detailed production model, with 60,000 to 70,000 hours spent there where I think his total earnings were in the low hun- 16 Maritime Reporter & Engineering News • January 2021
MR #1 (1-17).indd 16 1/7/2021 4:14:38 PM