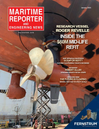
Page 32: of Maritime Reporter Magazine (January 2021)
The Ship Repair & Conversion Edition
Read this page in Pdf, Flash or Html5 edition of January 2021 Maritime Reporter Magazine
REPAIR & CONVERSION “We made the mistake in the past by having different vendors supply equipment. The integration is always dif? cult, and on a retro? t like this, it’s one of the biggest deals. It’s inevitable that if you have multiple vendors with multiple equipment there is always a problem, but it’s always ‘his problem, not mine.’”
Paul Mauricio,
Port Engineer
Copyright: Scripps Institution of Oceanography your mapping sonars.” sonars, you’re going to get junk. The ship is the instrument.” “Ships like Roger Revelle are very broad and not super long; so it pitches a lot,” said Appelgate. “As it goes through Cleaner Power the water pitching, it makes lots of bubbles and the bubbles The original ship contract value was for $35 million to take sweep down along the hull. Bubble masking is something care of speci? c ship systems – propulsion, controls, HVAC, that we understand very well now, but not so much back in piping, ballast water management – and steelwork to extend 1996. The place where all the transducers were (originally the life of the ship another 15 years or more, said Appelgate.
placed) were right in the place where bubbles would wash But “we knew that other issues on the ship needed to be down and, basically, wipe out your sonar signals.” addressed, or the primary users of the vessel just wouldn’t “In the period since then, there’s been a lot of work done on be satis? ed.” That’s where the upgrades to science systems how to mitigate that on a vessel without rebuilding the ship.” came in, adding another $25 million to the project.
The answer was a gondola that puts the transducers a few “The repower itself was intense,” said Mauricio. “We gut- feet below the hull “on a big metal structure that looks like ted the entire engine room and we pulled about six miles of a hammer head shark. (see page 37). It allows the bubbles cable, and we replaced about six miles of cable. There was to stay up next to the hull while the transducers are below not a square foot of that ship that wasn’t disturbed.” (For full them.” While the gondola was a boon for the science, it was technical details on the ship re? t design, see interview with one of the major design and construction challenges in the Tim Leach, Principal, Naval Architect (Glosten), on page 36) project. “Building that and then recon? guring all the cable “We ended up going with Caterpillars for our main engines, runs and moving the sonars down onto that thing was a big two 3516’s and two C32’s, running them at 1800 rpm,” said deal,” said Appelgate. Mauricio. “We put 2100 KW generators on the 3516’s and “You know, the ship is the science,” said Appelgate. “I cut 940 KW generators on the C32’s.” He said while the addition my teeth on making and operating sonars that were towed be- of the scienti? c gondola increased fuel consumption by about hind a ship. As we got better with sonars and motion sensors, 4%, the ef? ciency of the new machinery made it break even. those evolved into multi beams. Then we put them onto the “The biggest challenge with this project is the integration ship. Now, all of a sudden, the ship is your sensor. I think it’s of all new and existing systems,” said Benton Strong, Vigor, a valuable exercise to look at a ship holistically in that there’s the shipyard. “Nearly every major system was either replaced an instrument on the ship, let’s say a multibeam, that’s only entirely or upgraded signi? cantly, merging elements of new as good as everything that it’s attached to. Just like vibration, construction and ship repair into one cohesive project.” To if you’re transmitting a bunch of mechanical sound into your streamline the ? ow of information among multiple parties, 32 Maritime Reporter & Engineering News • January 2021
MR #1 (18-33).indd 32 1/7/2021 4:56:24 PM