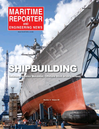
Page 44: of Maritime Reporter Magazine (August 2022)
The Shipyard Annual
Read this page in Pdf, Flash or Html5 edition of August 2022 Maritime Reporter Magazine
OFFSHORE WIND
Stiesdal A/S’
TetraSpar was installed late last year and has so far had 59% capacity.
Photo courtesy Stiesdal A/S big turbines will get.” build 30 maybe 50 ? oaters in a year. Even with 20MW tur-
However, volume wise, “We’ve not done enough and we’re bines we might be able to get anywhere from 500 – 1,000 not doing enough,” says Stiesdal, and that’s largely to do the MW out per year from such a shipyard. But there are very governments of the world choosing not to take the climate few that can do that. That’s why we’ve developed an indus- issue as seriously as they should have done, he says. “They trialised approach.” should take action with the same urgency as they did through the Coronavirus pandemic,” he says. “It’s like the tragedy of Stiesdal’s TetraSpar the commons. You had common areas around villages that Stiesdal’s ? rst ? oater, the TetraSpar, was installed off Nor- were not tended properly because they were everybody’s and way late last year with a 3.6 MW Siemens Gamesa turbine. It therefore nobody’s. It’s not about research. We know what we features a keel that is ballasted offshore, to enable assembly need to do. We don’t have a technology challenge, we have in low-draft ports. A turbine tower manufacturer used to auto- an implementation challenge. We have a long tradition of mated mass fabrication of tower sections, Welcon, was used growth. But we need society to assist us with good port facili- to produce the structure’s tubular braces and tank sections. ties. With easy planning, with good infrastructure for turbine These were then easy to transport and simply pinned together, delivery and receipt of all the power that we will deliver.” Meccano-like, with no welding, at a Danish quayside. Total net assembly time was 2-3 days, compared with typically 2-3
Targeting ? oating months for welded structures, says Stiesdal. The company
Stiesdal is targeting that delivery with his Stiesdal Offshore, says this approach could reduce manufacturing time by 85- a division of Stiesdal A/S, which he set up in 2017. It’s tar- 90%. The structure was then ? oated and towed-out to 200 m geting ? oating offshore wind, harnessing the experience Hen- water depth offshore Norway last year. Since it was commis- rik has gained over the past 40 years, not least around mass sioned, late November, to the end of April, it’s recorded a 59% production. While turbines are now mass produced, with the capacity factor. Despite a few small niggles, that’s still above cost bene? ts involved in that, foundations are still built us- the 50% average for offshore wind, says Stiesdal.
ing the fabrication methods used in oil and gas and shipping, which aren’t suited to mass production and involve too many Targeting 15MW man hours and port space to achieve the volume that will be However, the next Tetra ? oater will host a 15 MW turbine needed, he says. That’s a limiting factor. and be on a semisubmersible substructure, due to the (undis- “If you look at the biggest shipyards in Europe, they can closed) shallow water depths it’s been ordered for. For Sties- 44 Maritime Reporter & Engineering News • August 2022
MR #8 (34-49).indd 44 8/1/2022 2:52:47 PM