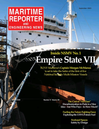
Page 33: of Maritime Reporter Magazine (September 2023)
Marine Design Edition
Read this page in Pdf, Flash or Html5 edition of September 2023 Maritime Reporter Magazine
THE SHIPYARD business case for these vessels, budget reviews and studies which stands for Evolving – being better than yesterday). We have were completed before the RFP was issued by TOTE Services. In a strong improvement program that captures input from every contrast to other government newbuild programs, the design was department in the shipyard and we spend a lot of time discussing essentially frozen when the RFPs were released, which enabled the input. For example, we look at employee retention, lessons us to understand the potential costs and risks of the program, as learned, how well we coordinate, how well our systems operate, well as optimizing the production ? ow to maximize ef? ciencies. etc. We are lifelong learners and are always trying to improve.
The wisdom of this approach has been con? rmed in the minimal changes we’ve seen during construction. To us, it has validated the bene? ts of the Vessel Construction Manager (VCM) structure for the construction of other vessels for the government.
How did Philly Shipyard invest in the yard, its equipment, speci? cally for this ship- building project?
The ? rst thing we had to do was to address the signi? cant amount of out? tting required for this vessel, something we had never experienced with product tankers and container vessels.
We had two large docks, sophisticated fabrication shops and a suitable yard layout for steel ? ow. What we didn’t have was a work? ow for an accommodation area to build cabins. This ended up being the largest investment we would make – a cabin fac- tory. We borrowed best practices from the cruise ship industry in
Europe to build completed cabins and lift them on board, rather them build them on board, and investing in a new cabin factory allowed us to do that. To accommodate the new cabin factory, we also added additional dry storage area for the cabin equipment.
Despite the best laid plans, ? rst ships of a series are always a challenge. What do you estimate was the biggest challenge to building Empire State VII?
Notably, the biggest challenge to building this ? rst vessel was the impact COVID had on both the workforce and the sup- ply chain, including material shipments. When we ? rst signed the contract in April 2020, at the beginning of the pandemic, no one could foresee the signi? cant long-term impact it would have. Ramping up the workforce, keeping safe and healthy operating conditions, handling the accumulating absences and supporting our workers through the pandemic was new terri- tory; and operating within those conditions was dif? cult for everyone. Although it seems to have lifted, the whole country is still feeling the effects and it could take years to fully recover from the many challenges we faced during the pandemic.
What are some of the lessons learned from the ? rst ship that can be applied to other ships in the series—or perhaps even other future new build programs?
One of the best opportunities with series-built projects is the opportunity for ship-to-ship improvement. This is something that has long been built into the culture here at Philly Ship- yard. It’s even re? ected in our CORE values (the “E” in CORE www.marinelink.com 33
MR #9 (18-33).indd 33 9/6/2023 6:24:23 PM