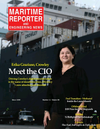
Page 24: of Maritime Reporter Magazine (November 2023)
Workboat Edition
Read this page in Pdf, Flash or Html5 edition of November 2023 Maritime Reporter Magazine
CTO IN FOCUS: DON HAIRSTON, AUSTAL USA ADVANCED TECHNOLOGIES
Image courtesy U.S. Navy
Additive Manufacturing to Support ‘One plus Two’
Austal USA Advanced Technologies is working with the US Navy on technical solutions that will power the next-gen of navy assets. Don Hairston recently took the helm of the AAT team, and discusses how additive manufacturing and arti? cial intelligence are powering the future of naval asset design, construction and lifecycle maintenance.
By Greg Trauthwein
Don, what speci? cally attracted you to the position as end capability is what we’re driving to support the US Navy
GM of Austal USA Advanced Technologies? with particular emphasis on the submarine industrial base.
I liked Austal USA as an up-and-comer; it offers tremendous growth opportunities. I also like the advanced technology as- In the context of AAT is doing for the Navy, what speci? - pect, especially in the additive manufacturing (AM) space. cally does additive manufacturing mean?
Our mission in AM is to support the submarine industrial base Today, the submarine industrial base relies on forging and in achieving the ‘one plus two’ goal … that’s construction of casting houses to provide mission-critical parts, and unfortu- one Columbia and two Virginia class submarines per a year. nately the existing industrial base cannot support the one plus
The only way we’re going succeed is through automation, a two cadence. Instead of growing the casting and forging indus- big part of which is additive manufacturing. It was appealing trial base footprint, we’re looking to expand and evolve that to me coming into Austal USA leading the Advanced Technol- footprint through additive manufacturing. We are leveraging ogy division, with a clear focus on the Navy’s Additive Manu- cutting-edge modalities for additive manufacturing such as facturing Center of Excellence in Danville, Virginia. laser powder bed fusion, direct energy deposition, friction stir processing and cold spray. Coupled with the different modali-
What are the key technology drivers of your primary cus- ties are various alloy types; our plan is to combine up to six dif- tomer – the US Navy? ferent alloy types with the appropriate modality to ensure that
If we look at the submarine industrial base, there is a grow- the right part is built with the right process and the right alloy. ing need for people, processes and automation, to support the Essentially, we are building the right “recipes”, in the form of growing scope of additive manufacturing; our partnership Technical Data Packages (TDPs), that prescribe an alloy type with the Institute for Advanced Learning and Research, also and AM modality for the industrial supply base to scale produc- located in Danville, is a key element for achieving the Navy’s tion of AM parts. The AM Center of Excellence is assembling one plus two requirement. Fundamentally, you need people, the TDPs for dissemination to a network of additive manufac- and the Institute brings a pipeline of highly-skilled, trained turers, and other machines within the network that we’re estab- operators in skills critical to manufacturing submarines. We lishing, to inject AM parts into the supply stream as alternatives have everything from training all the way through manufac- to forgings and the castings. We’re not going away from forging turing and part delivery co-located in Danville. That end-to- and castings; we’re supplementing production capacity.
24 Maritime Reporter & Engineering News • November 2023
MR #11 (18-33).indd 24 11/2/2023 9:11:53 AM