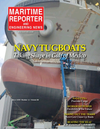
Page 56: of Maritime Reporter Magazine (November 2024)
Read this page in Pdf, Flash or Html5 edition of November 2024 Maritime Reporter Magazine
HEAT EXCHANGE tem to meet the needs of a wide range of operating conditions. the traditional Gridcooler Keel Cooler line to include, among
Existing cooling systems were far too large for landing craft, others, the WEKA Boxcooler, which was a development of so Robert developed a solution on his own. His compact keel Cees de Kwant in the Netherlands. cooler was the prototype for what would become our Gridcool- That early relationship with WEKA, in fact, was an impetus er Keel Cooler line.” to modernize its manufacturing. “Sean and Todd brought us out
As with any invention, the path to success is rarely straight of the dark ages with the manufacturing,” said Paul.
nor short, and the pressure from the Navy to develop a suit- Todd Fernstrum studied electromechanical engineering at able landing craft cooling solution was starting to frustrate the Michigan Tech, and initially he didn’t realize that his future young engineer. would be with the family business. An avid hunter, skier and “My father was feeling pressure from the Navy with the snowmobiler, he knew he did not want to relocate south, and his landing craft problem. They needed a hull type heat exchang- summers during college were spent making money working in er, and the only thing that was available was round tube with production at the family business. slip joints; the Navy didn't want that,” said Paul. “So he's in “Over time, I learned a lot about the processes, and I found the pump shop on a Saturday and he has this tube in his hand my niche in the production area and R&D, using some of skills and a mallet, and out of utter frustration he starts pounding on from my electromechanical side to develop some process con- this tube and it becomes oval. I think I could even feel today trols in the shop. This included changing a lot of the processes, the light bulb going off – that “Eureka” moment – as he found bringing in CNC machining and fabrication.” a way to have more tubes in a con? ned space.” The impetus for this change came in 2001 “when we part- “That ? rst model was 8 tubes wide and 54 inches long from nered with WEKA to start producing box coolers here for the nozzle to nozzle; it was very small on landing craft. It proved Americas,” said Todd. “At that point, we didn't have any in to be a very sturdy type heat exchanger and the Navy liked it, -house machining, and we were looking at having that done so they ordered many units for landing craft, and eventually outside.” Todd led the charge to bring in that ? rst CNC mill, extended the size and types of vessels,” said Paul. which at the time appeared well suited for future growth. “But things just keep getting bigger and bigger” and the heat loads
Investing in the Future grew, too, so it added another machine last year, and is eyeing
Central to its future is continued investment in the company: additional production equipment to make the processes even facilities, equipment, products and people, “but not necessar- more ef? cient and effective.
ily in that order,” Sean said. “The investment in facilities and “In the last few years, about $3 million of new equipment has equipment are obvious, the investment in product and people hit the ? oor,” said Todd, “but we're already at the point where perhaps not so obvious.” we're starting to think about upgrading and replacing some of
This investment has manifested itself also in a broadening of these machines to help increase capacity.”
Crew of an early test boat.
Rows of ? nished marine engines,
Gray Marine. All image courtesy R.W. Fernstrum & Company
MR #11 (50-65).indd 56 10/25/2024 2:52:24 PM