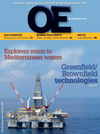
Page 41: of Offshore Engineer Magazine (Mar/Apr 2013)
Read this page in Pdf, Flash or Html5 edition of Mar/Apr 2013 Offshore Engineer Magazine
EPIC – Platforms
MHN Process platform: major system capacities.
Sr No S ystem Capacity Specifcations Remarks 1 Well fuid handling 2,700,000b/d - HP & LP Separators 2 Oil handling 47,750b/d 1% BS&W MOL pumps 3 Gas compression 6.9mmscm/d 7.5 to 97kg/sq cmg 3 trains 4 Gas dehydration 8.8mmscm/d 7 lbHO/mmcm TEG based 2 5 Sour gas sweetening 1.7mmscm/d Reduce HS to 40ppm from 2000ppm MDEA based 2 6 Produced water conditioning 2,250,000b/d 7 Living quarters (150 person) 8 Utility systems to meet the process, safety and operational requirements 9 Flare system for HP, LP and acid gas.
healthy interaction between all addition the jacket design had to East deck and West deck. The disciplines. The team size and be adjusted to changes in topside MNP deck further supported fve diverse locations added another weights (partly engineered). heavy modules: including building dimension. The project clocked Normally, jackets are designed module, process gas compression 17 million safe man-hours across based on inputs for topsides. (PGC) and one gas dehydration unit disciplines and locations. The However in this project, engineers (GDU) – gas sweetening unit (GSU). solutions were implemented had to design jackets with limited To transfer this load to eight jacket and installation activities were data. The jacket design was updated legs, three heavy cantilever support completed before onset of monsoon and optimized based on inputs for frames were also required. The in phase two. topside weights. conceptual design of MNP platform Completing the launch jacket was developed along with the
Engineering engineering within the available installation contractor.
L&T Valdel Engineering (LTV) time was a daunting task, This construction was achieved carried out engineering for MHN starting from conceptualizing the by integration of basic and detailed project. The main challenge was installation sequence, location, engineering activities from L&T’s to execute design and engineering shape and size of buoyancy multi-centered engineering teams of the entire process platform tanks, connection details, safety with daily monitored project complex that included FEED and integrity of jacket during schedules and close coordination and detailed engineering. All the installation, and a host of other with external agencies and vendors activities were to be performed parameters that had to be decided along with the project management concurrently with procurement before fnalizing the design. These team. and fabrication without affecting activities required co-ordination the overall project schedule and amongst various disciplines and Procurement milestones, while meeting ONGC’s teams. The MLQ jacket weight Mega projects require large stringent requirements. In addition, and lift radius was reaching the quantities of materials including review and approval of engineering capacity of the planned installation structural, piping, cables, documents from Aker Engineering barge, LTS 3000, necessitating equipment, and other items.
Malaysia and ONGC design team optimization of lift weight and Procurement scope included more were also required. design. than 300 equipments, 80,000 To give a perspective of the Living quarters weighing tonnes of structural steel, 50,000m structural challenge, the operating 4000 tonnes was optimized into in of piping, more than 10,000 valves topsides weight of the MNP Process single piece collaboration with M/s and pipe fttings, and 650km of
Platform was about 26,500 tonnes Specialist Services. This was the cables. To ensure competitive with a jacket launch weight of about frst time such a large module and prices and delivery schedules, 13,500 tonnes, while the living LQ was engineered. the procurement team decided to quarters topsides operating weight Due to the large weight of MNP source items from global vendors. was about 8400 tonnes with a jacket platform and complex feld layout, Many of the packages were lift weight of about 2260 tonnes. a foatover deck was not feasible. fabricated in-house and managed by Engineering faced many It was decided to fabricate the the team. challenges during the MHN project. platform in 10 modules. The MNP Major packages were fabricated
The jacket had to be delivered deck included South East deck, at MFF Hazira in order to meet 12 months ahead of topsides. In South West deck, North deck, delivery schedules and quality. oedigital.com March 2013 | OE 43 oe_EPIC_rev2.indd 43 27/02/2013 11:50