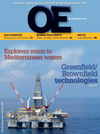
Page 42: of Offshore Engineer Magazine (Mar/Apr 2013)
Read this page in Pdf, Flash or Html5 edition of Mar/Apr 2013 Offshore Engineer Magazine
MNP jacket fabrication MFY Oman
MNP jacket had all the complexity vs – planned actual. that an eight-legged jacket can have.
The outside legs had double batter, whereas the inside (launch frame) was single batter, with 23 pre-installed risers on the jacket
EPIC – Platforms including one CRA clad riser, huge buoyancy tanks on side panels, and large sump caissons. The fabrication sequence was reviewed and optimized to arrive at the fnally accepted sequence, which
This included the GDU & GSU standards and strict discipline at optimized resources and had the package integrated into one module the project site. lowest fabrication cycle of weighing 1700 tonnes. Other Periodical HSE inspections were 10.5 months.
packages fabricated at Hazira carried out by offcers/engineers Major changes in boat-landing included primary and secondary and line managers to ensure a design and a change from three to
FG skids, and the produced water safe working conditions. Any four steps were also accommodated conditioning system package. defciencies found were rectifed during later fabrication stages. This was the frst time that a with top priority. Mammoet was involved in skidded
GSU package was installed on load-out of this jacket and the same an ONGC platform. This posed Fabrication was carried out smoothly. The many challenges, frst to prepare Fabrication was carried out extent of planning and execution the functional specifcation, in-house at Hazira and Oman and of MNP jacket fabrication is shown followed by approval of specifc involved 13 million man-hours above.
vendors. This was done by regular without any major loss time interaction with ONGC’s Offshore incident. At peak, more than 6000 MFF Hazira
Engineering Services. personnel were working at MFF While L&T Oman was working to Hazira. fabricate the MNP and MLQ jacket,
Health, safety & environment Apart from managing the MFF Hazira was also working to
The HSE department ensured that workforce, managing material meet fabrication requirements. all personnel were given safety quantities was a large task involving In 2010/11, MHN Project needed induction before mobilization quality requirements, storage, delivery of two fare jackets (750 and after reaching the worksite. material tracking, and timely tonnes each) and piles for all jackets
This included safety induction of allocation. Action was required to (13,500 tonnes). In addition, the subcontractor personnel, vendors, procure small quantities of material work had started on phase two etc. This helped maintain safety on an urgent basis. structures for MHN Project (33,500 tonnes), MHN PGC Project (5000 tonnes), and MNW-NF Project (500 tonnes).
Quality assurance and inspection
Apart from employing regular quality assurance and control, quality was also confrmed and emphasized by being proactive.
Material and equipment were categorized based on criticality ratings. Representatives conducted inspections at every stage to ensure quality.
Innovation and adoption of new techniques was considered a key factor, providing leverage to the tight project schedule and commitment to continual
MNP jacket sail-out from MFY Oman.
OE | March 2013 oedigital.com 44 oe_EPIC_rev2.indd 44 27/02/2013 11:50