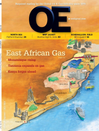
Page 28: of Offshore Engineer Magazine (Jul/Aug 2013)
Read this page in Pdf, Flash or Html5 edition of Jul/Aug 2013 Offshore Engineer Magazine
Remote caisson
Remote Technology inspection gets a hand he deterioration and failure of vehicle) deployment subsea is now the
Caisson inspection can caissons, and associated sup- industry’s preferred method, as diver be crucial for long term ports, is a core industry concern deployment has inherent safety risks
T for several reasons. Key is the impact and is also costly due to the require- integrity, especially of such deterioration can have on produc- ment for a dive support vessel. tion. Should the frewater pumps be frewater systems. adversely affected or out of action, the
The MAG-Rover platform is required to shutdown. Sonomatic has recently carried out
Graham Marshall,
Caissons can suffer degradation that several caisson inspections using subsea project manager, can lead to catastrophic failure if left its MAG-Rover, a tethered crawler
Sonomatic unchecked, with potentially severe system capable of topside and subsea health, safety, and environmental deployment. consequences. Given the number of The standard MAG-Rover unit is aging structures in operation, there is a a steerable crawler driven by two growing focus on caisson integrity. magnetic drive wheels, which allow
Repairs are costly and operators the scanner to attach to any magnetic have indicated that they require effec- surface. At the front is the ultrasonic tive inspection programs to identify transducer, which gimbals to fol- and address deterioration before the low the contour of the surface being structural integrity of a caisson is inspected. compromised. This involves regular It was originally designed for the inspection to assess the condition of inspection of monopiles using time caissons so that maintenance decisions of fight diffraction (TOFD). This can be made. involved mounting the tool on the internal surface of the monopole whilst topside, and driving it down the
Inspection
Before an inspection, it is diffcult to monopole to the subsea environment. assess the condition of a caisson visu- A straight line weld inspection probe ally, as one of the main degradation ensured the collection of consistent mechanisms in caissons is internal. data for analysis. Adapting this process
This makes external visual inspec- to carry out caisson inspections was tion a relatively ineffective method of relatively simple. determining the extent of deteriora- To use the MAG-Rover for caisson tion. Internal inspection is often not inspection, the tool was required to possible for pump caissons without a attach to the external surface of the shutdown to remove the pumps. caisson. The original design of the tool
External ultrasonic inspection is included capability for TOFD weld and an option that has many benefts, pulse echo inspection. though it too is challenged by the This capability was unchanged, but position of the caisson, which spans additional functionality was added subsea, splash zone and topside to enable corrosion mapping. This boundaries. As a result, the inspec- involved the adding a corrosion map- tion equipment involved must be ping third axis to fully quantify the capable of both subsea and topside thickness profle of the caisson. For inspections. ROV (remotely operated caissons, the MAG-Rover is attached by an ROV and controlled remotely topside. It is fully deployed by ROV
MAG-Rover deployed for caisson with no diver intervention. Once inspection.
OE | July 2013 oedigital.com 30 030_OE_0713_MF1_MagRov.indd 30 6/25/13 1:04 AM