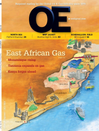
Page 38: of Offshore Engineer Magazine (Jul/Aug 2013)
Read this page in Pdf, Flash or Html5 edition of Jul/Aug 2013 Offshore Engineer Magazine
The MNP jacket sailed out from L&T’s
Modular Fabrication Yard in Oman.
dimensions were preliminary, tubulars with standard length of 11.8m and can length with extra 0.3 m were procured.
EPIC — I ndia
Schedule optimization:
The jacket was intricate, including 20 skirt legs with skirt pile guides, and 23 internal risers (over top and bottom row instead of side panel).
Jacket dimensions required the outside panels to be fabricated elsewhere, and
Fabricating to be moved to the fnal roll-up loca- tion after roll-up of the inside panels.
Self-propelled, modular trailers were an 8-leg launch jacket in record time used for transportation of panels. The fabrication sequence was altered four
Using multiple work centers and close project management, times to optimize activities and timing.
L&T delivered the MNP jacket on schedule.
Fabrication
Client representatives at LTV during
By C. S. Kole, Larsen & Toubro MFY LLC, Sohar, Oman engineering reduced cycle time and
Kumar Rudra, Larsen & Toubro, Mumbai, India speeded document approval. Client’s arsen & Toubro (L&T), India was on jacket weight. consultants were authorized to expe- awarded the Mumbai High North Due to time constraints, the project dite the work. Difference in time zone (MHN) process platform, living team decided to start fabrication based and work week between Oman and
L quarters, and process gas compres- on drawings submitted to the client India was effectively utilized for query sor module project by ONGC, on 31 for approval. Construction engineers resolution. The fabrication sequence
July 2009. The demanding, 33-month were available for real-time inputs on optimized use of resources during fab- schedule included EPCI of an 8-leg drawings. rication cycles. Its fexibility motivated launch jacket weighing in excess of The steel required was ordered from the construction team to innovate and 13,500 metric tonnes (mt) with jacket Korean mills, based on the preliminary try possible options. Special tools and delivery in 12 months. material take-off (MTO). Since the welding processes (automatic FCAW)
The project management team were used for launch cra- decided to execute the MNP Jacket dle welding and internal project from multiple work centers stiffener insertion inside with independent task forces: the main leg.
engineering at L&T Valdel (LTV) The jacket’s outside legs
Bangalore, fabrication at L&T Modular had double batter, whereas
Fabrication Yard (MFY) Sohar, Oman, the inside (launch frame) and project management and installa- had single batter. The main tion at Mumbai. jacket was to be supported
The MNP jacket (60m x 82m x 81m) on the seabed with 20 and its piles were completed ahead skirt piles and guides. The of schedule, in ten months. This was dimension between the achieved by meticulous planning two launch legs was 20m. and coordination between teams, and This jacket was divided “imagineering” unique fabrication into multiple compo- sequences. The MNP Jacket sailed nents including: launch away in November 2010. cradle (two per launch
Preliminary calculations indicated leg), launch truss (Row 2 a substantial increase in jacket weight & 3), side panels (Row 1 when compared to the client’s FEED & 4), Row A and B side calculations, due to an increase in panels, Five horizontal topsides area and load. Vendor inputs for equipment, packages, and installa- Mudmat fabrication in tion constraints had cascading effects process.
OE | July 2013 oedigital.com 40
EPIC4-India.indd 40 6/25/13 7:31 PM