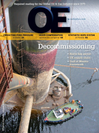
Page 65: of Offshore Engineer Magazine (Aug/Sep 2013)
Read this page in Pdf, Flash or Html5 edition of Aug/Sep 2013 Offshore Engineer Magazine
Subsea – Rope at great expense, the spar’s design allowing it to be used on a traction
Resolution includes a winch system that allows To solve the problem, Shell solicited system. Typically, the COF of steel the platform to service the subsea possible solutions from their winch ropes ranges from 0.05 - 0.08. The DPX equipment. Operating in nearly 9,000ft and cordage suppliers. After review- technology increases this to 0.1 - 0.15, of water, while handling payloads ing several proposals, Shell decided minimizing “slip” and damage.
of up to 90,000lb, is a challenge. a synthetic winch line offered many Synthetics also offer superior bend
Compounding the problem, the spar’s advantages and would require minimal fatigue properties than steel-wire rope design places the winch on a cantile- deck space. at smaller bend ratios. This feature vered deck (a smaller deck extending Shell turned to Samson for high- allowed Logan to design the winch sys- out from the main platform), imposing strength, lightweight synthetics and to tem with a smaller diameter traction signifcant weight restrictions. Logan Industries for a simple, traction- head, resulting in signifcant weight
A traditional steel-wire rope of this style winch design. This combination reduction.
length would be prohibitively heavy. met the weight and footprint restric- Since there was no heave compensa-
Weighing 81,750lb, it would require tions of the cantilevered deck and tion needed, cyclic bend fatigue was double the lifting capacity of the was capable of performing the subsea not a concern. Another advantage that winch. This would in turn increase operations, Figure 3. synthetic ropes have is a natural damp- the size of the winch and require sig- Samson provided 9,200 ft of 2-1/2in. ing effect that helps minimize package nifcant structural modifcations to be -diameter, Quantum-12 HMPE rope. motions (vs. steel). Steel-wire rope made to the spar. Weighing 85% less than a wire rope acts like a spring, transferring vessel
Another, and more signifcant, issue of similar size and length, this greatly motions to the package. A synthetic was the winch capacity. When using reduced the deck weight needed. rope has hysteresis, which provides steel-wire rope, signifcant winch Samson also worked closely with energy dissipation that minimizes capacity is consumed by the wire Logan Industries, assisting the design transferred motions. Figure 4 shows weight. The deeper the job, the longer engineers in creating a smaller, lighter the “looping” effect as a synthetic rope steel-wire rope is needed, and the less winch system specifc to the rope’s is cycled.
capacity the winch system will have. characteristics. To date, the system has performed
This means that the winch would The rope provides the same strength 250+ operations without any issues. have to be larger to accommodate the as similarly sized wire rope. It is made The original rope is still in service.
needed pay load at depth. with Samson’s patented DPX fber
A synthetic rope is buoyant; there- technology for superior abrasion and
Jubilee feld fore, it adds no weight to the payload, cut resistance with a higher coeffcient The Jubilee feld off Ghana, West regardless of length. The weight does of friction (COF) than other HMPE Africa, is estimated to hold 1.2Tcf not change (signifcantly) regardless of ropes. The higher friction coeffcient is of gas and 1.8 billion bbl recover- depth, Figure 2. an advantage over other HMPE ropes, able crude oil reserves, making it
Fig. 2. Buoyant, synthetic rope adds no Fig. 3. Lightweight, synthetic rope allowed use of a simple, traction-style winch to weight to the winch payload, regardless meet weight and space restrictions on a cantilevered deck.
of rope length or operational depth.
Fig. 4. Synthetic rope’s “looping” effect shows the positive effect of hysteresis, which dissipates energy to minimize transferred motions.
oedigital.com August 2013 | OE 67 066_OE0813_Subsea2_Rope.indd 67 7/22/13 10:11 PM