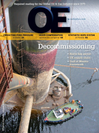
Page 66: of Offshore Engineer Magazine (Aug/Sep 2013)
Read this page in Pdf, Flash or Html5 edition of Aug/Sep 2013 Offshore Engineer Magazine
with a 12-strand core strength member made with high-strength, low-stretch
Dyneema fber. The jacket is made with polyester that grips the winch and hardware, and is abrasion resis- tant. To ensure that the rope would
Subsea – Rope sink rapidly enough to avoid catching in tugboat propellers, a segmented lead-line was added to the center of the 12-strand braided core. The addition of the lead allowed the rope to slowly sink out of the way of the propellers.
The specifc gravity increases from 1.01 to 1.12.
Once the customization and manufacture were complete, the line underwent extreme scrutiny. It was initially break tested, witnessed by the American Bureau of Shipping
Fig. 5. Jubilee feld used synthetic rope for anchor- (ABS). Then Technip, the project chain tensioning and riser pull-ins.
managers for the installation, com- missioned a study by Bureau Veritas (BV), who found the rope to be more the second largest feld in the world. light weight, abrasion resistance, and than adequate, with a safety factor of
First oil was produced in December neutral buoyancy to innovative rope 3:1.
2010, after risers and umbilicals were constructions and coatings. The light installed from the seabed at depths weight and “fexibility” of the syn- With these certifying agencies’ of 900-1700m to the FPSO Kwame thetic ropes would make handling approval, Samson manufactured three
Nkrumah, which successfully com- much easier in a small space. The lines for the Jubilee riser pull-in job. 1 7 pleted the fastest ever, full-scale, weight would be / (14%) that of steel, Sofec planned to use one of the three deepwater development. Samson’s allowing the ropes to be handled by lines for the anchor chain pull-in and
Turbo-EPX synthetic rope was instru- hand. tensioning line. This left one for the mental in the 11-riser installation, but Technip was responsible for the ris- riser installation, and one as a backup.
not before AmSteel-Blue frst assisted ers and had some abrasion concerns as After further consideration of the with mooring the FPSO. the synthetic ropes were being pulled anchor-chain pull-in job, Sofec realized 5 8
Sofec was in charge of the design through the riser tubes, Figure 6. While that the signifcant 5 / in.-diameter of and installation of the turret for the SOFEC was confdent that the ropes the rope would cause the line to bear
Jubilee feld development. Included in would work well in both applica- against the cast-steel sidewalls of the the turret design was a winch system tions, the riser installation engineers at chain stopper’s internal cavity. Again, that would be used for two projects: Technip were not so sure. Sofec contacted SWOS, who recom- anchor-chain tensioning and riser pull- Because of the neutral buoyancy of mended a smaller diameter rope of ins, Figure 5. the synthetic ropes, Technip also was AmSteel material to pull-in the moor-
The company was concerned about concerned that the rope would catch in ing chains.
limited room on the FPSO deck. The construction vessel propellers, which SWOS provided 738ft of 3¼in.-diam- most effcient solution would be to use would approach very close to the eter rope with a soft eye on each end. a small winch for the riser pull-in sys- FPSO when the risers were transferred. This rope is able to handle a working tem. A synthetic rope solution would Samson put application engineers to load limit of 100 metric tons (mt) with simplify the winch design and allow work developing a solution. a 400mt minimum breaking strength, a smaller drum diameter to be used. SWOS and Samson engineers equaling a 4:1 safety factor.
Synthetic rope would also allow a size worked closely with SOFEC to under- reduction of the hydraulic power unit stand all of the nuances of this proj-
Results and the deck load. ect and equipment. The engineers In a typical FPSO mooring applica-
Sofec contacted SWOS, Samson’s determined that the best combination tion, both wire and synthetic ropes master fabricating distributor in of equipment would be a split-drum are used on a split-drum winch;
Houston, Texas, to discuss a synthetic winch with a working load limit however, the AmSteel-Blue rope rope solution for the pull-in lines. of 350 tons, loaded with 350m of 5 worked in place of both. The rope’s 5 8
Samson synthetic ropes for offshore / in.-diameter Turbo-EPX HMPE easy handling and change-out allowed applications are made with Dyneema rope, which has a minimum breaking engineers to simplify the winch-drum fber, which brings high-performance strength of 875 tons. design, and provided fexibility for characteristics such as high strength, This rope has a jacketed construction the nine-anchor-chain installation
OE | August 2013 oedigital.com 68 066_OE0813_Subsea2_Rope.indd 68 7/22/13 12:54 AM