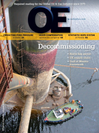
Page 67: of Offshore Engineer Magazine (Aug/Sep 2013)
Read this page in Pdf, Flash or Html5 edition of Aug/Sep 2013 Offshore Engineer Magazine
Subsea – Rope Fig. 6. Abrasion concerns were overcome by making the rope jacket from abrasion- resistant polyester.
and tensioning. The rope took quite a beating, but fnished the job without failure. Once the Kwame Nkrumah was secured in place, the Turbo-EPX rope was reinstalled on the winch and ready to pull in the risers.
Only one of the three Turbo-EPX lines was used to pull the 11 risers.
According to one Technip installation engineer, the rope was still in good shape after the job was complete.
These examples demonstrate how synthetic ropes can replace steel-wire ropes, creating more effcient and safer operations. One of the barriers to using synthetics can be initial cost. Synthetic ropes can be 2-4 times more expensive than wire rope. Therefore, it is impor- applications, and is still a tried and Justin Gilmore is technical sales manager tant to look at total cost of ownership true workhorse. Synthetic ropes, for the Offshore Business Unit of Samson and equipment cost. In most cases, however, should be considered when and has over 23 years in the synthetic when the total costs are compared, weight and handling become an issue. rope industry. He has an extensive back- using synthetic ropes can be more cost This is especially true for larger diam- ground in synthetic rope design, manu- effective. More importantly, synthetic eter ropes. In many cases, the user will facturing processes, quality programs, ropes are safer. fnd signifcant value in using high and application engineering with many
Steel-wire rope has a home in many performance synthetics. feld-related publications and patents.
Expert Access
Separation
Connect With Industry Experts
Live Presentation and Q&A
Technology 2013
What:
HMPE rope technology enables deeper and safer operations • Subsea Separation
The o