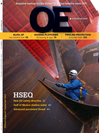
Page 110: of Offshore Engineer Magazine (Sep/Oct 2013)
Read this page in Pdf, Flash or Html5 edition of Sep/Oct 2013 Offshore Engineer Magazine
an environmentally sensitive area. This separation vessel performance lead- reduction in fowline pressures. The facility required good performance of ing to in specifcation separated effect was very dose-rate sensitive the primary separation vessels as being water and export oil. and care must be taken to not add n vital in ensuring standards were met Separator vessel internals (includ- too much chemical, due to the risk for produced water discharge quality ing inlet pipes, inlet device tubes, of water dropping out too rapidly,
Pipelines in addition to export oil quality. vane packs, and gas outlet demisting which would result in water accumu-
A series of studies were carried out devices) were critiqued and rede- lation promoting slug formation and to review the post-FEED (front end signed to improve performance. subsequent pressure fuctuations in n engineering and design) proposed An optimal emulsion treating temper- the fow lines.
n designs of production vessels (separa- ature range of 55-60°C was identifed New operational practices were put tors and an electrostatic coalescer) in and set in the design. in place to handle fuids from newly n the system, covering all aspects of ves- Hot water recycling to the frst-stage drilled fowback to host production sel designs that would affect separa- separator inlet from the second-stage wells, including optimized use of the tion performance, and later a review separator and coalescer was incorpo- slops tank.
study took place after operation of the rated in the design to aid separation system to help optimize performance performance and help keep the fuid
UK North Sea further. from being too near its emulsion-
A new oilfeld development in the
Discoveries were made at the design inversion-point zone of peak emul-
UK North Sea comprised of a 14°API stage and later after operation of the sion viscosity, which can hinder gravity heavy oil produced from feld on-site with recommendations good separation performance.
subsea wells to a FPSO required a full n implemented by the operator that led A revised subsea and topsides review of the critical fuid-sampling to an optimized separation system chemical application strategy was and production-chemistry characteri- design including: implemented.
sation data, to ensure that potential n n issues were identifed and incorpo-
Key emulsion stabilisers in the pro- Later trials of a subsea-injected rated into the production facilities duction fuids were found to be car- demulsifer indicated that it could design and development planning boxylate soaps, so demulsifers could decrease the fuid viscosity signif- be reformulated to directly handle cantly, while achieving some mod- process, so as to generate a ft for such components and improve erate increases in oil fow rate and One area of focus purpose design.
BOOST PRODUCTIVITY BY 30%
FLEXIBLE BLADDERS FOR:
OIL DISPERSANTS, METHANOL,
GLYCOLS, FUEL, LUBRICANTS,
HYDRAULIC FLUID, CHEMICAL
CLEANING COCKTAILS ®
Smart 3D
ACCELERATE PROJECTS AND GAIN A COMPETITIVE EDGE
Smart 3D is the next-generation 3D plant design solution for the offshore, process and power industries. It delivers at least 30% more productivity than any other system available today. The latest release of Smart 3D offers powerful rules and relationships that automate repetitive tasks, enforce design standards, ensure design integrity and protect design consistency.
LEARN MORE ABOUT SMART 3D?
ACCUMULATORS • ACTUATORS • BALLAST
COMPENSATORS • DAMPERS • DIAPHRAGMS
Come and visit us at Offshore Europe, Stand 3A115 from
FLOTATION • HYDRAULIC RESERVOIRS 3rd - 6th September 2013 in Aberdeen, UK
FUEL & BATTERY CONTAINMENT • PIPE PLUGS or send an email to: ® www. inc.com [email protected]
Tel: +1 201 825 1400 ®
Toll Free: 800 526 5330
Ramsey, NJ USA [email protected] © 2013 Intergraph Corporation. All rights reserved. Intergraph is part of Hexagon. Intergraph, the
Intergraph logo, and SmartPlant are registered trademarks of ntergraph Corp.
I
OE | September 2013 oedigital.com 112
Smart3DAd_OffshoreEngineer_SeptIssue_85.725 x123.825_C.indd 1 8/9/2013 3:39:27 PM 000_OE0913_pipelines_maxoil.indd 112 8/17/13 5:55 PM