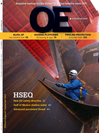
Page 82: of Offshore Engineer Magazine (Sep/Oct 2013)
Read this page in Pdf, Flash or Html5 edition of Sep/Oct 2013 Offshore Engineer Magazine
Mud on cuttings ranged from 1:2.20 to 1:2.72, while 1:1
Drilling waste minimation
Mud Cuttings is commonly accepted by the indus- 16/10-5 Isbjørn try as a very good ratio. However, the 400 ratio between solids and fuid was n
Total meters drilled (OBM): 1,976m reduced to 1:0.13, following the shaker n
Total drilling waste sent to shore: 300
Production replacement. 438mt
Waste and costs were reduced, due n
Total OBM added for priming of 200 to a reduction in the waste transported screw-conveyor: 62 mt (40cu m) Cubic meters ashore and reuse of drilling fuid. The n
Mud on cuttings: 27 mt (17cu m) 100 lifespan of the system’s flterbelt is 40 n
Mud on cuttings by stage: times longer than that of a traditional 0 15/12-A-07 A15/12-A-08 A15/12-A-17 BIsbjørn n 12 ¼” section : 5.4 wt% screen, from less wear on the surface n 8 ½” section : 12.6 wt% Well name system, pump liners, etc. n 16/10-5 Isbjørn well: 6.1 wt%
Comparing mud volume versus cuttings
Improvements in HSE conditions n
For each cubic meter drilled, 0.13 cu m volume for four wells shows how the were seen, particularly in noise, emis- n
OBM to cuttings ratio: 1:0.13 mudpump change reduced mud loss from sions, and vibration. Noise-levels were cuttings. reduced to 68dBA from about 95dBA, coupled with a continuously rotating well below the recommended 83dBA
Key goals
Previously, the Maersk Giant used four screen, offers high resistance to screen NORSOK standard for a 12-hour traditional shale shakers for primary blinding, minimizing the potential working day. Oil vapor and oil mist solids control. Following discussions for fuid to cascade off the unit and issues were completely eliminated in between Cubility, Maersk Drilling, into the drilling waste. Additionally, a the shaker room. Finally, there was
Talisman Energy Norway, and DONG secondary air-knife removes residual no need for structural reinforcement
Energy, these were replaced with three solids from the screen and deposits on the platform, due to the system’s
MudCubes. them in the discharge line. comparatively light weight and low-
Cubility and Maersk set three key After passing through a second- frequency vibration. goals to determine the success of the ary fltration system, clean fuid is A result of the project, workers on project: improving the shaker room’s separated from air and gas, through a the Maersk Giant have start calling the working environment, reducing the negative-pressure generating unit. The shaker room the “cube lounge,” due mud volume typically lost over stan- unit’s cyclone flter captures moisture to its emission-, noise- and vibration- dard solids control equipment, and and returns it to the active system. free environment. The Maersk Giant is minimizing the corresponding waste This recovery feature minimizes currently on contract to DONG Energy, volume, while improving overall drill- losses to evaporation and benefts the working on the Trym feld in the ing fuid performance. Throughout environment. Finally, the collected, Norwegian sector of the North Sea. the drilling process, these and other fltered, drilling fuid is deposited back parameters were monitored to assess into the active system via gravity fow. Asbjørn Kroken, vice the new shakers’ impact. president of engineer- ing marketing and
Results
Shaker differences
Maersk and Cubility had high expecta- sales, Cubility, has
The new shakers receive fuid and cut- tions for improvements in HSE condi- nearly 25 years of tings conventionally through a distri- tions and waste volume reductions. global experience in bution box. From here, the integrated The ratios between solids and fuid oilfeld services,
VCS processing technique takes effect. in the drilling waste on the Maersk focusing on new product and technol-
First, fuid is distributed evenly via Giant, when using traditional shakers, ogy portfolio management.
adjustable gates across a replaceable, non-tensioned, woven wire, stainless- steel screen (flterbelt), secured to a drivebelt, and vacuumed through the entire area of the flterbelt via a vacuum tray. Then, an air-knife blows on the wet cuttings and returns the fuid to the active system. While the unit does not shake, micro-vibration devices are employed to increase maxi- mum fow capacity.
As available screen openings are The Maersk Guardian covered by mud fow, air travels more jackup’s mudpumps were quickly through the remaining open- replaced with MudCubes.
ings. This increased air velocity,
OE | September 2013 oedigital.com 84 082_OE0913_ProdOps3-Mudcube.indd 84 8/18/13 11:39 PM