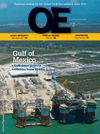
Page 66: of Offshore Engineer Magazine (Oct/Nov 2013)
Read this page in Pdf, Flash or Html5 edition of Oct/Nov 2013 Offshore Engineer Magazine
EonCoat is resistant to high temperature, abrasion, chemicals, UV sunlight, and other environmental factors.
New approach “What caught my eye about [CBPC
Pipelines coating] was its unique adhesion and chemical properties,” says Justice, who visited Wilson, N.C.-based EonCoat
LLC to view its corrosion testing lab, processes, and procedures for its
CBPC coating. “If its hard outer shell is breached or knocked off, it still has corrosion protection where traditional coatings do not. Whether its coating is aged, beaten, or banged around, it still protects the surface. If you remove the outer ceramic shell, the chemical bond with the substrate still stops cor- rosion at the surface.”
Ceramic coatings
In contrast to typical paint polymer coatings that sit on top of the sub- strate, the anti-corrosion coating bonds can prevent corrosion through a chemical reaction with the and tank maintenance contractor serv- substrate, and slight surface oxida-
Corrosion has long been the ing the oil and gas industry. tion actually improves the reaction. bane of the oil industry. Now
While traditional corrosion protec- This makes it impossible for corrosion new approaches and coatings tion has relied mostly on short-lived, promoters like oxygen and humid- physically-bonded coverings of sub- ity to get behind the coating the way are resolving the difculties and strate surfaces such as tapes, elaborate they can with ordinary paints. The providing intriguing possibilities three-part coating systems (zinc, epoxy, corrosion barrier is covered by a true for ofshore pipelines, explains and urethane), and cathodic protec- ceramic shell, which resists corrosion, tion, these merely attempt to lengthen fre, water, abrasion, chemicals, and
Tony Collins of EonCoat.
the time before the steel asset inevita- temperatures up to 1000°F.
n the oil and gas industry, corrosion bly rusts. While traditional polymer coatings accounts for over 25% of failures, Now a growing number of proactive, create a flm structure, which mechani- according to a recent National oil and gas industry maintenance pro- cally bonds to substrates that have
I
Association of Corrosion Engineers fessionals are turning to a new category been extensively prepared, if gouged, (NACE) International report. Corroded of tough, chemically-bonded, phos- moisture and oxygen will migrate pipe repair or replacement costs the phate ceramics (CBPC) that can pre- under the coating’s flm from all sides industry over US$7 billion per year, vent corrosion, extend equipment life, of the gouge. Moisture and heat are based on estimates from NACE. This and minimize the cost and production then trapped by the flm, creating a fgure can double when lost revenue, downtime required to recoat, repair, or “greenhouse effect,” promoting cor- productivity, and spill or leak cleanup replace corroded equipment. rosion and blistering. By contrast, the costs are tallied. same damage to the ceramic-coated
As deepwater exploration acceler- substrate will not spread corrosion ates, protecting offshore pipelines because the steel is essentially alloyed. from seawater corrosion is becoming Its surface oxides have been con- more vital than ever to preserve deeper verted into an inert, electrochemically and more costly oil and gas assets. stable metal incapable of supporting
While offshore pipelines supplement oxidation.
corrosion protection with cathodic Ceramic coatings such as this con- protection, the main defense against sist of two, non-hazardous ingredients corrosion remains external pipeline that do not interact until applied by a coatings, particularly fusion-bonded, plural-component spray gun like those epoxy-powder coatings. commonly used to apply polyurethane
EonCoat is a true ceramic coating that “Corrosion is a major industry chal- foam or polyurea coatings. Since the delivers a tough-as-nails, corrosion lenge,” says Scott Justice, Tank Division components are not mixed and do not resistant coating that can stand up operations manager of Bolin Enterprises meet prior to application, the need for to just about any application in the
Inc. (BEI), a Casey, Ill.-based pipeline hazardous volatile organic compound industrial or commercial sector.
OE | October 2013 oedigital.com 68 068_OE10130_Pipelines_Ceramic_Eon.indd 68 9/29/13 10:17 PM