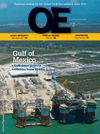
Page 67: of Offshore Engineer Magazine (Oct/Nov 2013)
Read this page in Pdf, Flash or Html5 edition of Oct/Nov 2013 Offshore Engineer Magazine
Pipelines (VOC)-generating ingredients is elimi- seasonally throughout the year, it can such as polyurethanes or epoxies, the nated, as are hazardous atmospheric be diffcult to provide perfect coating cure time may be days or weeks before particles and odor. This means that conditions.” the next coat of three coatings can be the work can be done in occupied Protective ceramic coatings can be applied, depending on the product. The areas. applied on hot or cold surfaces, from cure time is necessary to allow each “The results of the corrosion tank 40-150°F in 0-95% humidity, exclud- coat to achieve its full properties, even test were impressive,” says Justice. ing direct rain. though it may feel dry to the touch.
Among the corrosion tests frequently “Since the ceramic coating takes In contrast, ceramic coating is run by the manufacturer of the CBPC changes in temperature, humidity, and applied in a single coat, with almost product is one where the ceramic dew point out of the equation during no curing time necessary. Return to coating has gone more than 10,000 application, it can be reliably used in service can be achieved in as little as hours with no corrosion in a salt spray tough environmental conditions that one hour.
ASTM B117 test. “If the coating works might otherwise compromise the cor- “With the ceramic coating for cor- as well as we hope, it could help to rosion protection of typical coatings,” rosion protection, we’re able to get stop or minimize corrosion and extend says Justice. facilities back up and running right the longevity of a range of oil and gas away after spraying, sometimes in assets,” adds Justice. an hour,” says Bartko. “That kind of
Cutting downtime
Independent electrochemical cor- Shane Bartko, a director at TKO speed in getting an oil and gas facility rosion potential testing of the CBPC Specialty Surfaces, a Calgary, Alberta- producing again can potentially save product also indicates its usefulness based tank, pipeline, and structure millions per day in reduced downtime. for offshore pipeline corrosion protec- maintenance contractor, has used the It makes sense to use the ceramic coat- tion. Steel plates coated with EonCoat ceramic coating for corrosion control ing anywhere steel is used and may were placed in a beaker of saltwater on a variety of oil and gas projects. “To corrode, from pipelines and processing by Dr. Ki Yong Ann, Dept. of Civil and keep a corrosive coating working well, to storage.”
Environmental Engineering, in a lab you want one that will be resistant to at Hanyang University, Seoul, Korea. high temperature, abrasion, chemicals, Tony Collins is CEO
When voltage was run through the UV sunlight, and other environmental of EonCoat, LLC, con- solution and the corrosion rate deter- factors,” says Bartko. centrating his time mined by measuring current leakage The time saved on a corrosion coat- on commercial appli- across the coating in ma/sq m, the ing project with ceramic coating comes cations of Ceramicrete coated plates were found to have no both from simplifed surface prepara- technology. corrosion potential. Any result below tion and expedited curing time. “With Collins founded Turbine Generator “2” is considered to have no corrosion a typical corrosion coating, you have Maintenance, Inc., an independent potential, and the coated plates tested to blast to white metal to prepare the service provider for gas and steam at 1.15 the frst time, and 0.85 the surface,” says Bartko. “But with the turbines, in 1986 and sold it in 2007, second time. ceramic coating, you typically only after amassing customers in 47 states
For submerged offshore pipeline have to do a NACE 3 commercial brush and 15 countries. Collins earned a BS applications, an anti-fouling topcoat blast.” Bartko explains that on coating in Mechanical Engineering (1978) from can be added to the CBPC coating, projects using typical polymer paints Georgia Institute of Technology.
which enhances appearance and reduces barnacle growth.
Unlike organic, carbon polymer- based paints and coatings, which may give a foothold for corrosion causing microbes to grow, ceramic coatings are completely inorganic, so they are inhospitable to mold or bacteria. “Since
EonCoat is inorganic, it cannot sustain mold or bacteria growth,” says Justice.
While not widely considered, the
Achilles heel of many traditional cor- rosion coatings may be in how exact the environmental conditions must be
Corrosion is a major during their application to meet speci- industry challenge from fcations. “A lot of coating products external foating roof tanks, fail due to changes in temperature, to tank interiors, to above and below grade piping systems, humidity, dew point, and other atmo- particularly where pipes transition spheric factors during application,” from above to below grade.
says Justice. “As conditions change oedigital.com October 2013 | OE 69 068_OE10130_Pipelines_Ceramic_Eon.indd 69 9/29/13 10:18 PM