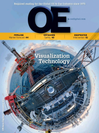
Page 48: of Offshore Engineer Magazine (Nov/Dec 2013)
Read this page in Pdf, Flash or Html5 edition of Nov/Dec 2013 Offshore Engineer Magazine
Safety
Ofshore installations service specialists. Photo: ABB.
Integrated Safety know they will work? What about the understand the risks? Did they use rea-
Integrated safety with automation sonable levels of probability? How about pumps? systems can be an important technol- the consequences? Did they mitigate
Safety Culture ogy trend where critical information or those factors?
Equipment will continue working for alarms are on display. Utilizing common Technology will not fx a problem unless years, but other factors intervene. Just reporting tools for safety and control the right processes and the right best how sure is everyone that valves that systems creates an environment for practices are in place. Technology will have been in place for 20 years or so consistent analysis and breeds familiar- help enable people to make the right will open or close as they should dur- ity with safety systems for the operator. decision. But the safety culture has to ing an emergency situation? Have they
Along those lines, operator ergonomics be there to enforce them to make the undergone any testing and how do you that facilitate fast and correct operator decision in the frst place. Even with decision-making and produces measur- multiple technology protective layers, able improvements in plant productivity,
Reducing Human Errors information fow, and safety can improve
Through a series of advances, the alarm failures and the lack of adequate the work environment and have a posi- sophistication of hardware and tive impact on remaining alert, which safeguards and use of outdated process software technology has advanced removes the potential to miss critical design. information due to fatigue.
tremendously over the past 30 years.
In addition, today’s technology would
The design allows for the system to
Through the use of automated proce- issue a warning or event indication that react properly to an incident, but it can’t dures, proper audit trails, management would be able to alert the operator or just stop there. Inevitably, operators need of change process, alarm management, maintenance workers if there was a recir- training. The system cannot prevent situation-based displays, human-cen- culation automated level control valve every little discrepancy, but the right tered HMIs and control room design, left closed or if there were failures or problem solvers in the right culture mar- humans still remain at the pulse of the breakdowns not attended where a work ried to the technology will solve issues design, operation or maintenance. order ended up closed without the job before they escalate.
It would be possible to reduce errors completed. In the scenario,
Piper Alpha
One way to deal with safety is to by keeping a focused eye toward asset if a safety valve was out for maintenance implement lifecycle management that optimization, where the user could eas- will not only allow the user to work with and Pump A was out of service there issues known today, but also take care of ily access procedures and confguration would have been warnings available at those that appear down the road.
guidelines. An integrated control and the system level and the automated log
Review the entire lifecycle. When the safety system would be likely to catch would have explained the situation to designers created the system, did they
November 2013 oedigital.com 50 048_OE1113_ABB Safety.indd 50 10/28/13 1:57 AM