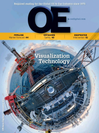
Page 50: of Offshore Engineer Magazine (Nov/Dec 2013)
Read this page in Pdf, Flash or Html5 edition of Nov/Dec 2013 Offshore Engineer Magazine
Safety
A man demonstrates how to use a 3D KPI Board. Photo: ABB.
• • Reduced costs, including maintenance Set up procedures for reducing inci- emergency relief valves, piping and pres- costs. dents that include proactive asset man- sure vessels, etc. undergo inspections at • Compliance with the ability to reliably agement and written standard operating defned frequencies.
• meet ever more demanding regulatory procedures. Alarm management. A root cause of • requirements Perform comprehensive hazard assess- the Three Mile Island nuclear plant
Technology backbone to a culture that ment after every incident or accident to incident was the operators ended up • ensures safety and integrity are integral ensure equipment meets baseline protec- swamped with alarms. Operators had parts of day to day operations. tion levels at minimum. dozens of fashing lights and they • •
Delivery of performance which means Manage process safety as an all-inclu- couldn’t tell the wood from the trees. a more proactive approach and managing sive effort where all parties (including Alarms need to be in context. Now there improved performance sustainably third-party contractors) possess appropri- are emergent standards coming out that ate process safety knowledge and exper- allows for a certain amount of alarms in
Continuous Training tise. Root cause analysis of incidents 10 minutes.
A majority of the industrial accidents that leverages lessons learned and adds to the Safety goes beyond just ensuring pro- occur every year are a result of human overall body of knowledge. cesses remain stable. By having a solid • error. Every year, a majority of accidents Consider an integrity management plan and ensuring a strong safety culture occur as a result of improper training of system to gain more knowledge of the where users and automation technol- personnel. Systems can have the right current state of all equipment as it relates ogy remain intertwined, there will be a design to react properly to an incident, to safe operations. direct link to increases in production and • but manufacturers need properly trained Do retrospective HazOp implementing decreases in incidents. Producers need workers to ensure the safe handling of a “what if” scenarios. If the plant has been to look at the big picture and realize just problem. running 10 to 15 years, every fve years what a strong safety program brings to
Manufacturers need to have an action the plant should do a HazOp test to make the bottom line. plan of best practices to ensure a safe sure everything is working.
• Layers of protection analysis (LOPA). environment. They need to: Luis Duran is Product
Marketing Manager,
This is to overcome human factors where plants undergo changes over the
Safety Systems, at
ABB. Duran holds a years. People have modifcations like
Expert Access add ons or close offs. This type of analy-
Functional Safety
Empower Ofshore
Engineer certifcation sis would inform what was working and
Operations with Human- what was not.
from TÜV, and an
Centered Technology
Asset integrity management. This is for MBA and a degree in •
December 12, 1 pm CT the mechanical items on a production Electrical Engineering from Universidad
See page 77 for details.
plant. Make sure the control valves, the Simon Bolivar Caracas, Venezuela.
November 2013 oedigital.com 52 048_OE1113_ABB Safety.indd 52 10/28/13 1:58 AM