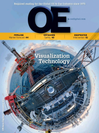
Page 68: of Offshore Engineer Magazine (Nov/Dec 2013)
Read this page in Pdf, Flash or Html5 edition of Nov/Dec 2013 Offshore Engineer Magazine
AN INTERIM SYSTEM FOR THE GOM sources of hydrocarbons, we made additional enhance-
Formally established in December 2010, MWCC ments to these initial capabilities to keep pace with provides containment technology to respond to a their needs. For example, in August 2011, procedures well control incident in the deepwater US Gulf of were developed to provide containment operations
Mexico. Today, the company is composed of ten for deepwater drilling wells under foating production members, all active in the GOM. MWCC’s contain- facilities (TLP/SPAR). These procedures were necessary ment system is available to to be able to install well containment equipment under any company planning to foating structures. Additionally in September 2012, the drill in the deepwater GOM, capping stack was upgraded for use at well tempera- either as a member or as a tures up to 350 degrees and pressures up to 12,750 psi;
T he operating non-member on a per well for higher pressures up to 15,000 psi, the temperature environment in the basis. As a company whose rating remains at 250 degrees.
purpose and mission is to
In July 2012, at the direction of the Department of
US GOM encourages be continuously ready to re- the Interior (DOI), MWCC initiated mobilization of spond, the capping stack is its interim containment system, including a physical technology develop- at the core of our response deployment of the capping stack. Working with mem- system. ber company, Shell Oil Company, MWCC successfully ment to meet the
MWCC has two capping conducted the demonstration on a simulated well in the stacks designed for use in the Walker Ridge block in the deepwater GOM. The demon- evolving needs of
GOM, and is currently building stration included deployment to a simulated wellhead in a third which will be delivered 6,900ft of water using the heave compensated landing operators. The need in 2014. The capping stack is system. All necessary functions were completed, and to move to deeper an integral part of our overall pressure testing confrmed the ability to control a well. containment system, and has This capping stack demonstration validated that the depths and greater come a long way since 2011. right equipment and processes are in place to safely
The frst capping stack is rated and effectively cap a well.
pressures may not at 15,000 psi and weighs 100 In January of this year, MWCC introduced a smaller tons. It provides a dual barrier 10,000 psi capping stack with a dual ram that is designed be too far off the for containment – a blowout to reach deepwater areas where well casing and riser preventer ram, plus a contain- systems are closely spaced. This smaller capping stack horizon. ment cap. This massive piece can cap a well in depths up to 10,000ft. The completion of equipment is about 30ft of the 10,000 psi capping stack – which stands 25ft tall tall including the necessary lifting gear, and 14ft wide. including the necessary lifting gear and weighs ap-
When frst introduced in 2011, the capping stack could proximately 50 tons – is an example of our collaboration function in 8,000ft of water, but was later confrmed with our members, listening to the needs and, in turn, capable of capping a well in up to 10,000ft and cap and meeting them. Its 9ft by 9ft frame makes it easier to fow a well in up to 8,000ft. The system has the capacity maneuver where wells are closely spaced such as ten- to handle up to 60,000 b/d of liquid, and handle up to sion leg platform (TLP) applications where wells are 120MMscf/d of gas. beneath a foating production facility. This 10,000 psi
However, as our members looked for new and deeper capping stack is another example of the evolution of containment technology and the ongoing enhancements to the overall system.
Marine Well Containment Company’s 10,000 psi capping stack stands
Photo: MWCC.
25ft tall and weighs approximately 50 tons.
AN EXPANDED SYSTEM
WITH GREATER FLEXIBILITY
As mentioned above, an expanded system is under development. Building on current system capabili- ties, an expanded containment system (ECS), which represents an investment of more than US$1 billion by the members of MWCC, is currently being built. The
ECS will provide greater fexibility to accommodate varying member needs, including greater contain- ment capacity and use in deeper water depths. The expanded system will build on current capabilities to cap and fow a well in up to 10,000ft and can handle up to 100,000 b/d of liquid, and handle up to 200MMscf/d of gas.
This system required a number of frsts for the indus- try including the deepest production risers (reaching 10,000ft water depths) and the shallowest free-standing adjustable risers (reaching 2,000ft depths) ever built.
Additionally, the subsea fexibles are the deepest ever oedigital.com
OE | November 2013REVIEW 70 068_OE1113_Dif_CappingSt.indd 70 10/28/13 3:46 AM