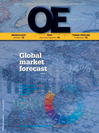
Page 42: of Offshore Engineer Magazine (Jan/Feb 2014)
Read this page in Pdf, Flash or Html5 edition of Jan/Feb 2014 Offshore Engineer Magazine
Fig. 1: Sandvik super-duplex tubing.
containing chloride have demonstrated that tubing made from ASTM 316L has a service life shorter than ? ve years and, in
EPIC some cases, less than one year.
This was based on ? eld trials con- ducted in tropical waters by Shell,
Swagelok, and BP, and laboratory testing by Sandvik.
Operational experience in tropical waters, such as the Gulf of Guinea and the
Gulf of Mexico, has mirrored test results, with ASTM 316L tubing service life seen at less than ? ve years. In some extreme cases, it can be less than one year.
One ASTM 316L test sample on a ? oat- ing production, storage and of? oading unit in the Gulf of Guinea showed severe signs of corrosion in small diameter tubing in several locations in the topside facilities, less than a year after the unit was moored in place. Low levels of
Molybdenum (Mo) in ASTM 316L steels was a contributing factor.
This has serious implications, not least the potential for accidents, causing injury, or worse, due to sudden failures, as well as the potential serious damage to the platforms.
In topside process systems—consisting of various vessels, heat exchangers, sepa- rators and compressors—poor equipment
Longer lasting life-spans pose a risk of sudden equip- ment failure, and may even lead to costly accidents.
Materials need to have resistance to super-duplex super-duplex stress corrosion cracking (SCC), pitting, such as beneath clamps, support trays, and crevice corrosion in chloride-bearing
Topsides corrosion and short and connections. Both pitting and crevice environments, in order to be suitable for life span issues, particularly in corrosion depend on chloride concen- hydraulic and instrumentation tubing tropical waters, are being tackled trations and moisture levels. They applications on offshore platforms.
can be further exacerbated by surface Some companies are turning to cor- with a super-duplex steel. contamination, caused by iron particles rosion resistant alloys (CRAs), ranging
Joseph Osta explains.
from welding and grinding operations, from grade 13Cr and upwards, as well surface deposits from handling, drilling as 6Mo austenitic steel types (containing rowing global demand for and blasting, and from sulfur-rich diesel 6% Mo), such as 254 SMO, AL-6XN, and energy is driving oil and gas engine exhaust. Even periodic testing of alloy 625. These cost more than super-
G companies towards deeper seawater ? re? ghting systems can leave duplex steels, because they have higher wells in more exposed locations. Such undesirable chloride salt deposits. levels of Ni and Mo, and there is lower environments subject offshore rigs and The normal lifecycle of ASTM 316L market availability. platforms to even greater threats of local- steels can exceed 100 years, in non-corro- An alternative to CRAs are super- ized corrosion. sive environments. Tests in environments duplex steels, which have higher
On offshore platforms, stainless steel strength, enabling a reduction in wall tubing is used in process instrumenta- thickness of tubes and pipes in hydraulic tion, hydraulic lines, chemical inhibition and instrumentation systems, reducing and utility applications. Many of these cost and weight.
Sandvik has developed a super-duplex applications are topside, and, in tropical waters, corrosion of ASTM 316L stainless
Fig. 2: ASTM 316L stainless steel and SAF steel tubing often occurs, primarily due 2507 super-duplex tubing, installed side to marine atmospheric corrosion. by side, with the ASTM 316 tubing showing
The result is mostly pitting and crevice extensive corrosion and the super-duplex tubing showing none. corrosion, often in inaccessible locations,
January 2014 | OE oedigital.com 44 044_OE0114_EPIC1.indd 44 12/19/13 5:28 PM