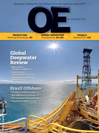
Page 108: of Offshore Engineer Magazine (May/Jun 2014)
Read this page in Pdf, Flash or Html5 edition of May/Jun 2014 Offshore Engineer Magazine
Sections of CRA-lined pipe are put through numerous physical tests, moni- tored by strain gages used to measure axial and radial force, and piezoelectric and Bourdon gages to monitor pressure.
Pipelines
Hydraulic rams, heating coils, and vari- ous other devices are then applied to sections of pipe to simulate the severe conditions at the bottom of the sea
Using test data, combined with indus- try-standard material properties for X65 pipe lined with 316L CRA, INTECSEA created Abaqus FEA models of their pipe and carried out parallel virtual tests.
Multiple simulation runs were performed using both pressurized pipe models replicating production conditions, and unpressurized ones that reproduce the conditions expected during transport and installation.
Image 3: Temperature is an important component in pipe performance and simulation models replicating such performance require accurate data capture. Here, a pipe is wrapped in a heating blanket as it is brought up to 130°C, replicating the efect of
Reducing both development costs high temperature well fuids.
and long-term risk
Results to date have been promising.
Ultrasonic tests show close correlation between FEA and real-world behavior, demonstrating that INTECSEA’s pipe and weld designs are performing well. Better yet, internal rippling of the CRA liner has been demonstrated to be minimal for certain design conditions, even when subjected to high buckling forces and temperatures of 130°C. (Image 5)
According to El-Gebaly, once the models have been fully validated, using
Abaqus will certainly help INTECSEA reduce real-world testing costs. But there’s more to it than higher front-end savings:
FEA helps to assess design risks and pos- sible failures. “For pipelines, it only takes one joint to fail for a release-of-contents event to occur, so it is crucial to assess
Image 4: CRA-lined pipe wrapped in insulating material. This test demonstrates a pressurized and heated pipe placed under a 1.5% strain load. every failure mechanism,” he said.
Image 5: A bird’s eye view—
Kip Hanson is a looking inside a heated pipe that freelance writer and has been reverse loaded with a manufacturing severe bending strain. Several consultant in Tucson, ripples can be seen in the upper left hand corner of the photo.
Arizona. With more
Images from Paul Montague.
than 30 years’ experience in the wrinkling onset conditions, manufacturing and as well as the fatigue perfor- business management, he has written on mance of the girth weld during a wide range of topics, including the installation and design life,” machining and fabrication, consumer
El-Gebaly said. products, oil and gas, CAD/CAM/FEA and ERP systems. Prior to his current
A day in the life of lined pipe position, Kip worked as the IT director
Much of the data needed to for a global manufacturing company, and accurately capture such behavior also spent a number of years business with FEA models comes from consulting with a mid-range ERP extensive land-based testing. software and services provider.
May 2014 | OE oedigital.com 110 000_OE0514_pipelines1_intecsea.indd 110 4/19/14 9:54 AM