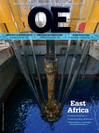
Page 29: of Offshore Engineer Magazine (Jul/Aug 2014)
Read this page in Pdf, Flash or Html5 edition of Jul/Aug 2014 Offshore Engineer Magazine
Analyzing wireless machine condition monitoring to offer effective wireless systems in the process measurement A safe solution for hazardous environments domain. The potential to improve effciency through condition moni- for ofshore applications
Compared to process measurements (scalar, overall values), toring has driven the development of a new wireless solution. vibration monitoring (dynamic data arrays) places unique The SKF wireless machine condition sensor monitors machine demands on wireless sensors, networks and associated compo- components in locations that are diffcult to access. It achieved nents: high bandwidth, good dynamic range, low noise, higher- ATEX Zone 0 certifcation, which means that it can be used in level processing capabilities and the ability to capture data at the hazardous environments.
right time. When operating as self-contained battery powered The SKF wireless machine condition sensor collects data on units, the further challenge of practical service life remained. three key machine conditions: temperature (indicative of lubri-
Morever, physically mounting the sensor device directly onto cation issues, increased friction, rubbing, etc.); overall machine a machine necessitated coping with the aggressive conditions condition (vibrations caused by misalignment, imbalance, found in the industrial environment, such as exposure to water, mechanical looseness, etc.); and rolling element bearing condi- extreme temperatures, electrical interference, hazardous area tion (allows damage detection and diagnosis of source as ball / classifcations, obstructions, and physical location/distance. roller, cage, inner or outer raceway).
Recent convergence of protocol standards coupled with new wireless condition monitoring technology developments have addressed these challenges, resulting in a viable solution. Next it is necesary to consider deployment options to gain wide acceptance.
Comparing methodologies
Condition monitoring of rotating equipment is a common throughout the oil and gas industry, with the objective to detect, analyze and diagnose machinery faults. Critical machines (tur- bines, compressors, large motors) are normally equipped with on-line condition monitoring and protection systems. Balance- of-plant equipment (motors, pumps, fans) generally are not. Yet this machine category represents well over half of the population and consumes a signifcant percentage of a maintenance budget.
Such machines are normally monitored manually with portable data collectors because it has been impractical or uneconomical to install a permanently wired system. However, the situation
Once data is collected, the WirelessHART gateway communi- has changed with the advent of a new breed of wireless condition cates with SKF’s wireless sensor device manager software.
feld-mounted signal acquisition system still required sensors to monitoring systems that bridges the gap between the cost wired be wired from machine to sensors. The system manages the con- systems and ineffciencies of portable systems.
Comparison of wireless systems version of data to digital form and then transmits it to the host
Integrating condition monitoring and process control data
PC wirelessly. This works well and there are thousands of chan-
Wif 900 MHzMesh Networks nels of vibration data being managed in this way. However, for Another important development has been the ability to share • • • Uses IEEE Uses the 900 Uses IEEE 802.15.4 the oil and gas industry-specifc requirements for installation data with process control systems. Changes in vibration levels 802.11g radio MHz public radio radio standard in areas with hazardous gaseous environments prohibited most may be due to a change in operating conditions, and without standard band • WirelessHART protocol applications due to the requirement for packaging of the system that knowledge an incorrect diagnosis could be costly in terms • • Commonplace in No radio stan- or ISA 100.11a ofces, hotels and dard, but ofered in expensive explosion-proof enclosures. of down time and lost production output.
• Early adoption phase homes, and well by many smaller
Meanwhile, the promise of ubiquitous, low-cost process mea- In the past, passing data such as temperature, fow and load, in industrial settings understood. It is companies (mainly oil and gas) at surement sensors operating over a wide area has fuelled mas- between the condition monitoring system and the process not so common in using a propri- sensor data level sive investments by wireless technology and process measure- control system was time-consuming and complex, involving industrial settings etary protocol and methodology • Self-generating network ment companies. Widespread market adoption did not initially dedicated serial communication links and cumbersome data • High data rates reduces installation cost occur due to technical issues such as proprietary protocols and protocol programming. Today, the emergence of OPC (OLE but high power Low data rates • consumption with medium power Low data rates but low • installation cost barriers. With recent advances in network- for Process Control) has reduced this task to a few “click and consumption power consumption ing, radios, processors, sensors, and power sources it is now drag” operations between networked computers. This has had • Low to moderate point- Longer point- Low to moderate • • possible to overcome these obstacles with process measure- a signifcant impact on the analyst’s ability to correlate vibra- to-point range to-point range point-to-point range ment devices. And, with the emergence of standard wireless tion changes with process conditions. All of SKF’s condition (e.g. 100m) (e.g. 300m) (e.g. 50 – 100 m) protocols, increasingly advanced systems have been developed monitoring software platforms can utilize OPC.
oedigital.com July 2014 | OE 31 030_OE0714_Feature2_SFK.indd 31 6/20/14 11:47 AM