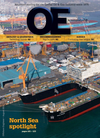
Page 68: of Offshore Engineer Magazine (Aug/Sep 2014)
Read this page in Pdf, Flash or Html5 edition of Aug/Sep 2014 Offshore Engineer Magazine
Additional informa- tion is shown on an alphabetic display.
Between 28-35mm-
EPIC diameter rope can be tested, at 0.5-3m/s rope speed, and temperatures ranging from -40°C to +50°C, Slasarev says, with the magnetic head able to be up to 80m from the control and display unit. Sensitivity is down to one external wire, with the loss of metallic cross-sectional area (LMA) measure- ment accurate to less than 2%, says Slesarev.
Rope condition estima- tion criteria is based on
LMA, the maximum broken wire density value, and the incre-
Fig. 4 Intron’s Intros Auto magnetic head. Photo from Intron. ment of broken wire density relative to the rope or better controlled splicing meth- NDT previous inspection.
Innovations in how to test wire rope ods could help, he says. Further, the
Roughness offshore, on drilling rigs and offshore break load when using alternative ter- cranes, were presented by Moscow- Herbert Weischedel, NDT Technologies, minations on the sling ends also needs based Intron and US-based NDT US, says more than LMA and localized to be understood. The new standard will not address braided slings used in
Technologies. faw (LF) inspection is needed to prevent the US and Asia, as they’re not used in
While standard magnetic rope testing early retirement of high-value wire rope.
Europe, due to not being manufactured remains a core necessity, an automatic The frm has developed an additional in the region.
rope monitoring system could provide method to defne wire rope deterioration,
In fber, there is no standard instant information for operators, offers called wire rope roughness (WRR). This describing the certifcation process
Intron’s R&D director Dimitry Slesarev. is an aggregate surface roughness of all for sling capacity, it is up to the user
Magnetic rope testing has been in use wires in a rope, caused by and indicating to do certifcation, although the new for more than 30 years. Sensors measure interstrand nicking, at wire crossovers,
DNV-OS-H205 gives some guidance, magnetic fux leakage, caused by mate- internal broken wires, and corrosion pit-
Breedeveld says. “Fiber is new and rial discontinuity. But, Slesarev says, ting, usually within the frst and second different from steel. We need to know this type of testing requires qualifed layers of the rope, Weischedel says. what fber it is, what design, yarn personnel, results can be complex and Electromagnetic wire rope inspection strength, other empirical factors. Even require interpretation, and conventional methods include LMA, a quantitative then, how much material is actually inspection methods mean having to stop analysis, which is used to assess inter- in the string is unknown because the operations. nal and external corrosion and wear, by manufacturer will not always say. High “So we have developed an automatic measuring loss of metallic cross-sectional performance fber is a reliable product system, that is rugged, permanently area, and localized faw (LF) inspection, for offshore lifting operations, but the installed, simple to service and use, and a qualitative analysis to detect external certifcation process is an issue,” he giving reliable inspection results and auto- and internal discontinuities, such as says. An IMCA subgroup is working matic processing of data,” Slesarev says. single broken wires and corrosion pitting. on a guideline for the design, use and
Intros-Auto comprises a control However, there can be signal ambiguity inspection of high performance fber and display unit to be handled by the in LF inspection, as, while the signal slings.
operator, which will be connected to a rises for single broken wires, it falls when
Where small diameter steel or fber magnetic head placed on the rope just there are clusters of broken wires. rope is used for lifting applications, above the winch. Intros-Auto can be used NDT’s WRR assessment uses the frm’s the break load is based on full scale with or without distance counter, it can own computer assisted rope evaluation break tests, which is not practical on be also connected to external computer, software to do quantitative analysis of the large diameters. Can you use computer for real-time monitoring and additional LMA signal. To avoid downtime on facili- modeling to avoid all this testing, asks analysis. Rope condition is indicated on ties using rope, NDT has developed a non-
Breedeveld, adding that more research is the control and display unit by a tri-color, contacting, continuous rope monitoring needed. LED system, red, yellow, and green. system (CRMS), incorporating WRR.
August 2014 | OE oedigital.com 70 000_OE0814_EPIC4_OffshoreLift.indd 70 7/22/14 10:20 PM