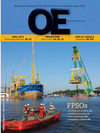
Page 48: of Offshore Engineer Magazine (Sep/Oct 2014)
Read this page in Pdf, Flash or Html5 edition of Sep/Oct 2014 Offshore Engineer Magazine
The Baker Hughes
SlickBit anti-balling SlickBit anti-balling one driller by 68% in water-based mud
Kymera FSR directional Kymera FSR directional coating technol- coating technol- (WBM) over the same bit, uncoated, run hybrid drill bit creates hybrid drill bit creates ogy. The coating ogy. The coating on a sidetrack of the same well. They fewer torque long ago proved its long ago proved its also observed that a coated bit in WBM ? uctuations and tolerates more value in preventing value in preventing drilled 72% faster and 3.5 times longer
Drilling weight on bit for bit balling but was bit balling but was than the average of uncoated bits in faster drilling.
sometimes lack- sometimes lack- OBM in this area. The same operator, ing in durability. ing in durability. in a different area saw bits coated with
Now an enhanced Now an enhanced the improved SlickBit coating drill- ? ouropolymer- FSR bits also incor- ? ouropolymer- ing 57% faster in WBM without shale based compound, porate a new line based compound, balling, compared to offsets in OBM. maintaining the of tungsten carbide maintaining the And in a 54 bit sampling of bits in one
SlickBit designation, cutters in its design. cutters in its design. SlickBit designation, area in Alaska, prone to shale balling, is much tougher and The new generation of The new generation of is much tougher and the coated bits drilled 45% further. more durable than its cutters is sharper and up cutters is sharper and up more durable than its With this new BHI bit coating, BHI says predecessor due to the to 30% tougher than the pre- to 30% tougher than the pre- predecessor due to the operators are now seeing signi? cant cost addition of novel reinforce- vious lines leading to higher vious lines leading to higher addition of novel reinforce- saving through fewer bit trips, reduced ment additives, says Steven ROP and reduced vibration. ROP and reduced vibration. ment additives, says Steven NPT, faster ROP, and eliminating the
Radford, technical advisor. By Current Kymera FSR bit applica- Current Kymera FSR bit applica- Radford, technical advisor. By cost and challenges of using oil based applying the SlickBit coating to tion has been primarily onshore, tion has been primarily onshore, applying the SlickBit coating to mud. however, expansion to commercial the drill bit, cuttings are less likely
Halliburton offshore application will begin in about to adhere and ball up, allowing the six months, Holliday says. driller to drill faster and longer, reduc- Set to launch early in the coming year,
BHI has also recently commercial- ing bit trips. Application in the Gulf of Halliburton Drill Bit Services’ new cutter ized a new line of cutters, the StayCool Mexico has shown increased ROP for technology will boast higher abrasion multidimensional resistance, impact resistance, and ther- cutter. In design for mal mechanical properties, according to nearly two years, and Brad Dunbar, product manager for Fixed introduced in October Cutters Drill Bits for HDBS.
2013, the StayCool With the use of data from offset wells, cutters are constructed engineers were able to identify areas of with a groove in the improvement and re? ne their designs body. In contrast from with the ultimate goal of producing more the shearing motion of ef? cient drill bits with the capability to the traditional smooth drill longer intervals and a higher rate of faced cutter, the grooved penetration. contour of the cutter Changes in the chemistry and manu- produces a scooping facturing processes used to develop motion. By introduc- this new technology have resulted in a ing the groove to the number of new patents. Featured along-
Baker Hughes’ StayCool multidimensional cutter technology cutter design, the cutter side proven technology, the new cutters
Images courtesy of Baker reduces the drilling day curve and costs.
Hughes.
produces less frictional have increased its abrasion resistance by heat which results in 20-30% as compared to previous prod- less thermal degrada- ucts, Dunbar says.
tion, longer durability, In terms of removing thermal mechani- and greater ef? ciency of cal, abrasion, and impact damage as the bit. In comparison, barriers to performance, “the goal of PDC the StayCool cutter runs manufacturing is to push those three about 50% cooler than boundaries,” Dunbar says.
Development for the yet-to-be-named its standard counterpart
PDC cutter began nine months to a year in laboratory testing, ago, and it is currently in the validation and similar results and testing phase. For the purpose in ? eld applications; of collecting larger amounts of data increases in average in a shorter amount of time, current
ROP, about 15%, and application of the new technology is average footage drilled, limited to onshore sites. However, about 12%, have also when the new product line, featuring been seen, says Barzin the new cutters, is released, interested
Chiniwala, cutter prod- companies can expect them to be uct manager.
Baker Hughes’ StayCool multidimensional cutter technol- marketed for both onshore and offshore
Improvements have ogy minimizes friction on the cutter face, improving rates drilling operations. been made to BHI’s of penetration.
September 2014 | OE oedigital.com 50 048_OE0914_D&C1_overview.indd 50 8/21/14 4:10 PM