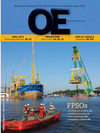
Page 47: of Offshore Engineer Magazine (Sep/Oct 2014)
Read this page in Pdf, Flash or Html5 edition of Sep/Oct 2014 Offshore Engineer Magazine
stabilize the bit in the hole and reduce the hole to be drilled larger, but also also be customized for a speci? c motor. If
Drilling vibration, increase stability, steerablilty results in the bit cutting unevenly. For progress continues as expected, commer- and durability resulting in lower repair over three years, the Bent Housing Motor cialization of the new product may begin charges as well. project engineers have been developing a 4Q 2014.
With greater energy focused on the solution. Understanding the issue, NOV After continuous improvement, NOV cutters they must be able to ef? ciently engineers have developed a proactive has also re-introduced the FuseTek drill manage the in? ux of energy. Now approach, whereby the bits are designed bit. A hybrid that incorporates both PDC standard in all Tercel ? xed cutter drill to adapt to the non-axial rotational move- and diamond impregnated technology bits, the Phoenix premium PDC cutters ment and cut the formation accordingly. into the same bit, the FuseTek bit is meets this challenge and improves upon Using NOV’s in-house software, models designed to drill zones that are interbed- previous standard cutters in both shock of how the drill bit rotates are con- ded with hard and soft layers. By com- and abrasion performance. Operators no structed, allowing the path of each cutter bining the two technologies, engineers longer need to choose between improving to be traced. Individual cutter contact have increased the durability of the bit. impact shock or abrasion resistance. The with the formation is then modeled so The PDC cutters can cut through the soft
Phoenix series cutter allows simultane- that the cutter layout is optimized. This layers until they eventually fail as the ous improvement of both properties, produces a directional bit that cuts all bit drills hard layers. Then, the diamond prompting better ROP performance, lon- portions of the bottom of the well and impregnated portion continues to drill ger depth drilled and less repair charges. in a more predictable manner. During through the harder lithologies. This will
Produced using “low cobalt content, the tests in the Epping Field, North Dakota, save the driller from unnecessary non- [cutters] strength is really in [perform- the new design produced more footage productive time when tripping in and ing] in a dynamic thermal environment,” than the offset well using a competing out to replace bits. At an offshore well
Morrissey says. bit. The new bit is designed to work with in the Iwafuneoki Field in Japan, during
Application of the new product line a broad base of motors, however, it may 4Q 2013, application of the FuseTek drill face of the bit. By improving the energy has seen success in three subsalt wells bit saw a 174% increase over the average distribution to the more ef? cient cutters, in a development project off the coast interval drilled by competitor bits in the the weight on bit is used more effectively of Brazil, outperforming competitor same well, and an 84% increase in foot- in the cutting process, resulting in an drills bits in the same formation. Future age over the next best performing bit.
average increase in ROP of 36-40% and application will likely be seen in offshore
Baker Hughes up to an 82% increase in recent Bakken ? elds of Malaysia.
shale applications, says David Morrissey, Baker Hughes Inc. (BHI) has been busy
NOV
Vice President of Sales and Marketing. this last year introducing and develop-
The design may be applied to any ? xed
At NOV, product development is often ing new technology for the oil and gas cutter drill bit. The MicroCORE cutting an evolutionary process, says Tony industry.
Watts, engineering manager. A perfor- BHI will add to its unique line of structure removes the inef? cient center cutters on the bit, develops a core by mance issue is identi? ed, analyzed, and hybrid drill bits with the introduction a solution is developed. One problem of the Kymera FSR. The hybrid drill cutting around the center of the hole, and provides an ef? cient method of evacuating
ReedHycalog has identi? ed facing drill- technology was ? rst introduced in 2011 the undisturbed core fragments to surface. ing engineers is the eccentric and off-cen- to target hard interbedded formations.
Trace of cutter movement during ter drill bit motion on bent housing motor Having succeeded in their original
These core fragments never see the shear- eccentric and o