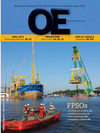
Page 46: of Offshore Engineer Magazine (Sep/Oct 2014)
Read this page in Pdf, Flash or Html5 edition of Sep/Oct 2014 Offshore Engineer Magazine
Drilling
Breaking barriers
Jerry Lee discusses new and improved drill bit designs and technologies with several leading companies
The MicroCORE Bit, developed in collabo- The MicroCORE Bit, developed in collabo- The MicroCORE Bit, developed in collabo- MicroCORE cuttings are not impacted ration with TOTAL, allows the continuous ration with TOTAL, allows the continuous ration with TOTAL, allows the continuous by the shearing process of the cutters generation of micro-cores, while drilling. generation of micro-cores, while drilling. and provide an undisturbed structure for
The core, broken by the bit, is carried to The core, broken by the bit, is carried to analysis in any formation type. Photos from the surface through the annulus along
Tercel Oil? eld Products Ltd.
with the drilled cuttings.
face of the bit. By improving the energy distribution to the more ef? cient cutters, who have introduced or are develop- the weight on bit is used more effectively ing new drill bit technologies and in the cutting process, resulting in an innovations to overcome some of average increase in ROP of 36-40% and those challenging issues facing the up to an 82% increase in recent Bakken industry today.
shale applications, says David Morrissey,
Vice President of Sales and Marketing.
TercelTercel The design may be applied to any ? xed
Tercel Oil? eld Products Ltd. has been Tercel Oil? eld Products Ltd. has been cutter drill bit. The MicroCORE cutting testing and qualifying its latest innova-testing and qualifying its latest innova- structure removes the inef? cient center tion since 4Q 2013. Improving upon their tion since 4Q 2013. Improving upon their cutters on the bit, develops a core by ising energy demand has resulted in cutting around the center of the hole, and previous MicroCORE designs, Tercel’s previous MicroCORE designs, Tercel’s
R the need to reach reserves in more provides an ef? cient method of evacuating product line, featuring the new Phoenix product line, featuring the new Phoenix complex formations. The more complex the undisturbed core fragments to surface. cutters, began commercialization in the cutters, began commercialization in the the formation, the more issues that arise These core fragments never see the shear- last couple of months.
that must be addressed before produc- ing action of the cutters and provide a high
Though the MicroCORE design has tion can begin. Those complex challenges quality sample for analysis on the surface.
been around since 2007, Tercel’s innova- must be met by similar caliber innova- tion is focused on enhancing the rate of Tercel’s ? eld tests have shown that tion and development from the industry. penetration (ROP) performance by opti- the process of drilling the core and the
Currently, there are several companies mizing the arrangement of cutters on the more ef? cient cutting structure work to
Onshore ? eld test in North Dakota
MicroCORE v. standard drill bit
ROP
MP813 8 1/2NA142014 with and without 1.20E+01 50100150200250 40mm MicroCORE at same WOB, Std goes 0 9.14m/h and MCB at 12.96m/h Graph of 1.00E+01 cutting surface distribution per cutter 2,000 8.00E+00
Tercel MicroCORE 4,000 6.00E+00
Tercel Standard 6,000 4.00E+00
Measured depth 2.00E+00 8,000 0.00E+00 10,000
Competitor (O