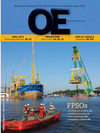
Page 59: of Offshore Engineer Magazine (Sep/Oct 2014)
Read this page in Pdf, Flash or Html5 edition of Sep/Oct 2014 Offshore Engineer Magazine
controller, which is a real-time super- SWOB set point to deliver the desired extend drill bit and BHA life and reduce compromising safety or the reliability of
Drilling visory control engine that utilizes rig DWOB determined by the drilling the number of expensive trips due to the equipment. High-speed downhole equipment to deliver the desired DWOB. program plan or optimization applica- bit or downhole tool failure. In harsh data means the rig and drilling sys- •
Well construction applications tions. Auto driller parameters such as drilling conditions and complex drilling tem can be used in a less conservative The add-on does more than just RPM and differential pressure can also environments, the system can deliver way—the equipment can be pushed to a enhance control; it enables data visu- be recommended by the optimization knowledge and performance to help con- higher limit because of clear visualiza- alization and software applications. applications. tractors and operators achieve their goals tion of the downhole environment. This 3.
Current applications deliver rate of The autodriller receives the SWOB safer and more ef? ciently,” Pink says. safe and controlled lack of conservatism penetration (ROP) optimization, risk set point as a request, analyzes it in the The system has been through three could signi? cantly improve well deliv- management, dynamics mitigation context of its current operational state onshore ? eld tests and it has been used ery times and reduce the cost of ? eld (SoftSpeed II stick-slip service), and and safety case, and makes a decision on two onshore commercial wells. development.” steering optimization. whether to implement the requested “The early results have demonstrated Three major projects are being planned in Norway with Total, ENI, and Lundin.
The data ? ow and automation process is SWOB set point or not. that these technologies can deliver as follows: The NOV DDS optimization team has signi? cant performance improvements,” 1. Data from the BHA and drillstring are already demonstrated consistent ROP Pink says. “The largest observed bene? t This article is based on a presentation by transmitted to the surface via the telemetry improvements of 20-30% with occasional however was more cultural than techni- Tony Pink, National Oilwell Varco, pre- network and combined with surface data improvements of 100% (Pink et al. 2011). cal; the high-speed downhole drilling sented in March 2014 at the SPE work- in the rig’s control system. The data is vali- “Drilling automation improves drill- dynamics data allows the driller and shop, In Arctic Norway, and a presenta- dated and analyzed on a ? xed time interval. ing stability, reduces risk, and increases the customer representatives to maxi- tion at the IADC’s conference in Vienna
Control logic computes the required ROP. These improvements will also help mize the performance of the rig without in June 2014.
2.
NOV’s Closed loop drilling system oedigital.com September 2014 | OE 61 060_OE0914_D&C4_NOV.indd 61 8/21/14 4:50 PM