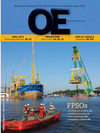
Page 64: of Offshore Engineer Magazine (Sep/Oct 2014)
Read this page in Pdf, Flash or Html5 edition of Sep/Oct 2014 Offshore Engineer Magazine
obtain well fow, an important factor for monitoring.
Standard measurement methods cur-
As the industry advances into rently being employed on rigs are mostly ultra-deepwater, an increasing achieved using a fow paddle and the
Well surveillance
EyebrowProduction active volume. Measurements based on number of tight tolerance wells the fow paddle can be easily obtained, require an efcient system for but paddle reliability is low due to its in ultra-deepwater determining early infuxes or mechanical principle and the noisy signal, especially on foating rigs where losses during drilling, tripping, heave is a signifcant factor. Moreover, and cementing operations. Scott comparing the signal with pump fow rate also is not possible. The accuracy of
Hilliard of Statoil and Florian the measurement from the fow paddle
Le Blay, Soufan Berhil and is debatable. The fow paddle provides
Eric Villard of Geoservices, a fuid height measurement, but requires an assumption of the fuid veloc-
Schlumberger company, present ity in any attempt to infer a fow rate. a new early detection fow
Unfortunately, the fuid fow profle can change signifcantly with fuid properties monitoring system and setup for like density and rheology.
foating rigs.
The advanced measurement process in this paper includes many factors that can ith the increase in ultra- infuence the measurement of actual fow deep, high-pressure high- including pump rate, pipe movement,
W temperature (HPHT) wells, mud compressibility effect, fow line fow new drilling technologies are crucial. back and heave effect.
Differential fow out, which is the differ-
Monitoring active pit volume and the ence between actual fow out and theoreti- mud level in the fow line are standard cal fow out, allows for accurate and quick ways to detect infux or “kick,” the most
As part of the FLAG service, a Coriolis fowmeter installed in the return fowline calculation of the actual volume of the dangerous hazard encountered during continuously measures the actual fow. Photo from Schlumberger.
infux or loss without being affected by pit drilling HPHT wells in ultra-deep water. transfers that happen often during drilling.
However, detecting gains or losses using man. With the time required for detecting the electromagnetic sensor make it the
Early gain detection is the frst advan- the active pit is delayed due to the length infux and the infuence of the commu- best option for fow measurement, being tage of using fow measurement at the fow of the fow line and the communication nication chain, additional volumes can restricted to conductive fuid, or water- line. Detecting infux as early as possible is chain on the rig. build up before the decision is made to base mud (WBM), made the Coriolis fow crucial to reducing volume and minimiz-
Active pits are commonly located far shut in the well. sensor the preferred option because it ing the risk of an uncontrolled event, or from the wellhead at the end of the fow works with any kind of drilling fuid.
Sensor types spending time controlling the well.
line after the gumbo box and shakers. Pit However the Coriolis fow sensor was transfers and other operations can infu- The use of the fow paddle on the fow rarely used because it required heavy
Case study ence the volume and require constant line to detect gains and losses has installation and was available only in communication between the driller, mud shortcomings, so in the 1990s, improved a small 6in. size. The installed sensor Figures 1, 2 and 3 demonstrate real-time loggers, mud engineers, and the derrick fow sensors were introduced on some requires a bypass setup. Its small size lim- data from a kick event on a sixth genera- rigs to measure fow from the well more its the fow rate by inducing a signifcant tion drillship in 2500m of water drilling accurately. Two types of sensors are now pressure drop that leads to a hydrostatic a 12¼-inch section. The curves plot- common: the electromagnetic sensor and head before the bypass. This hydrostatic ted on the charts have been drawn and the Coriolis fow sensor. head reduces the fow rate. displayed in real time during a drilling
The introduction of larger Coriolis
Although the size and confguration of operation in which a kick occurred.
sensors in recent years
The kick occurred at 7 p.m., the deci- has raised the limit of the sion to stop the pumps was made at 7:10 maximum fow rate. When p.m., and fnally the well was shut in combined with an opti- at 7:20 p.m., recording a shut-in casing mized bypass design, these pressure of 450psi. Some maintenance large sensors can be used at was performed on the Coriolis sensor very high fow rates for all during the well control operation, which drilling operations as long explains the fow measured by the sensor as drilling fuid return is after the well has been shut in.
directed into the fow line.
Figure 1 compares the measurements of the fow paddle with the differential
Measurement methods fow out based on the Coriolis fow sen-
Accurate measurement of sor. The plot highlights the fact that, if
Fig. 1: Comparison fow paddle vs. diferen- tial fow out. Images from Statoil and Schlumberger.
return fow is required to the rig had been equipped with only the
Fig. 2: Comparison pit volume vs. diferential fow out.
September 2014 | OE oedigital.com 66 066_OE0914_ProdOps_2_SLB.indd 66 8/21/14 1:29 PM